Reliability-Centered Maintenance: Complete AI-Powered Guide for 2025
Jun 6, 2025
RCM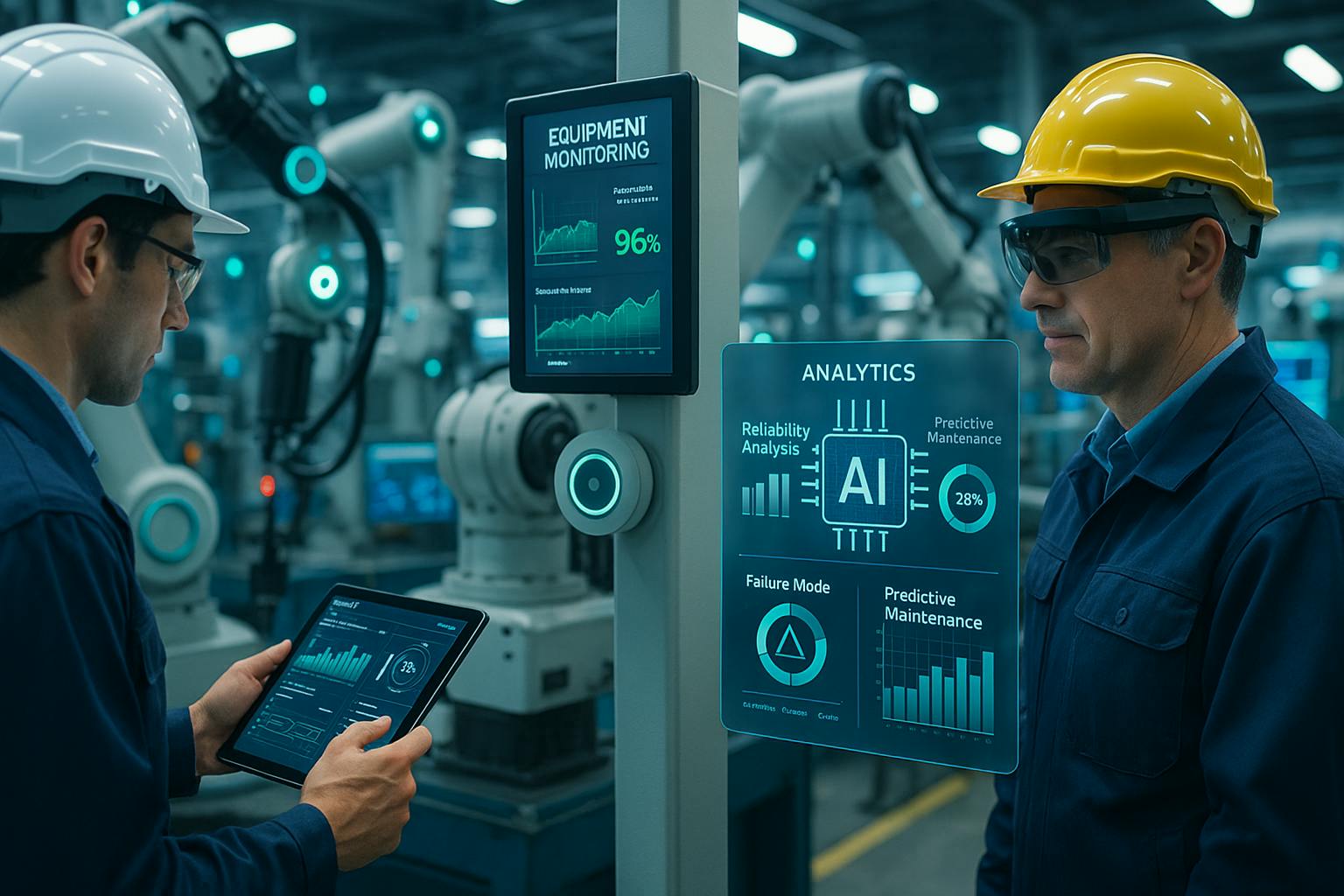
Reliability-centered maintenance (RCM) represents the most systematic approach to equipment maintenance strategy development, yet 70% of traditional implementations fail to deliver promised results. As manufacturing enters the Industry 4.0 era, artificial intelligence and digital technologies are revolutionizing how organizations implement and optimize RCM programs. This comprehensive guide explores how modern AI-powered approaches overcome traditional limitations while delivering superior reliability outcomes and measurable ROI.
What is Reliability-Centered Maintenance?
Reliability-centered maintenance (RCM) is a systematic methodology for determining the most effective maintenance approach for any physical asset based on its function, failure modes, and consequences of failure. Unlike traditional maintenance strategies that focus on preserving equipment condition, RCM prioritizes preserving system function through evidence-based decision making.
The foundation of RCM lies in understanding that not all equipment failures have equal impact on operations. By analyzing what functions equipment must perform, how it can fail to perform those functions, and what happens when it fails, organizations can develop maintenance strategies that optimize reliability while minimizing costs.
Key principles of reliability-centered maintenance include:
- Function-focused approach: Maintaining capability to perform intended functions rather than preserving equipment condition
- Failure consequence evaluation: Prioritizing maintenance efforts based on failure impact severity
- Risk-based decision making: Allocating resources where they provide maximum reliability benefit
- Continuous optimization: Regular review and refinement of maintenance strategies based on performance data
Modern RCM implementation has evolved significantly from its 1960s aviation origins. Today's RCM 4.0 approaches integrate artificial intelligence, IoT sensors, and advanced analytics to overcome traditional methodology limitations while delivering unprecedented reliability improvements.
The Evolution of RCM: From Traditional to AI-Powered
Traditional RCM Challenges
Classic reliability-centered maintenance methodology, while technically sound, faces significant implementation challenges that contribute to the 70% failure rate. Resource intensity represents the primary barrier, with traditional RCM analysis requiring 6-18 months for complex systems and teams of specialized facilitators.
Common implementation obstacles include:
- Analysis paralysis: Overwhelming detail in FMEA documentation without clear action priorities
- Static assessments: Point-in-time analysis that doesn't adapt to changing operational conditions
- Skills dependency: Heavy reliance on expert facilitators and cross-functional team availability
- Integration complexity: Difficulty connecting RCM outputs with existing CMMS and maintenance workflows
- Cultural resistance: Challenges transitioning from reactive to proactive maintenance mindsets
The RCM 4.0 Revolution
Artificial intelligence and digital technologies are transforming reliability-centered maintenance from a resource-intensive methodology into a dynamic, data-driven optimization platform. AI-powered RCM addresses traditional limitations through:
Automated failure mode identification using machine learning algorithms that analyze historical maintenance data, sensor readings, and operational patterns to identify emerging failure modes without extensive manual FMEA sessions.
Real-time risk assessment through continuous monitoring and dynamic prioritization based on current operating conditions, equipment health indicators, and production schedules.
Intelligent task optimization leveraging predictive analytics to optimize maintenance timing, resource allocation, and task sequencing for maximum reliability benefit.
Continuous learning systems that automatically refine maintenance strategies based on performance outcomes, failure patterns, and changing operational requirements.
Core RCM Methodology and Standards
The Seven Questions Framework
Reliability-centered maintenance follows a structured seven-question framework that guides systematic analysis from functional understanding through maintenance task selection. This proven methodology, codified in SAE JA1011 standards, provides the foundation for both traditional and AI-enhanced implementations.
Question 1: What are the functions? Functions define what users want assets to accomplish in their present operating context. Primary functions relate to main operational purposes, while secondary functions cover protective devices, control systems, containment, structural integrity, safety, environmental compliance, comfort, and appearance.
Question 2: How can it fail? Functional failures occur when assets cannot fulfill required functions to desired performance standards. This includes total function loss, partial degradation, excessive energy consumption, or inability to meet quality requirements.
Question 3: What causes failure? Failure modes describe specific events or processes that cause functional failures. Modern AI-powered analysis can automatically identify failure modes through pattern recognition in maintenance history, sensor data, and operational logs.
Question 4: What happens when it fails? Failure effects describe what happens when specific failure modes occur, including immediate consequences, secondary effects, and ultimate impacts on safety, environment, operations, and economics.
Question 5: Why does it matter? Failure consequences determine maintenance strategy selection. Hidden failures require scheduled tasks to ensure protective function availability. Safety and environmental consequences mandate proactive tasks. Operational and economic consequences justify cost-effective maintenance approaches.
Question 6: What can be done? Proactive tasks include predictive, preventive, and detective maintenance activities. Each task must be technically feasible and worth doing based on consequence severity and task effectiveness.
Question 7: What if nothing works? When no proactive task proves effective, run-to-failure strategies may be appropriate, potentially combined with redesign, operational changes, or one-time changes to reduce failure consequences.
SAE JA1011 Standard Compliance
The Society of Automotive Engineers JA1011 standard establishes minimum criteria for processes claiming to be reliability-centered maintenance. Compliance ensures systematic analysis quality and provides credibility for RCM implementations.
Key compliance requirements include:
- All seven questions must be answered in sequence for every significant item
- Functional failures must be identified for each function
- Multiple failure modes may be identified for each functional failure
- Failure effects must describe what happens when specific failure modes occur
- Maintenance tasks must be clearly defined with specific intervals and criteria
Modern AI-powered RCM platforms can automatically ensure JA1011 compliance while reducing manual effort required for documentation and analysis.
Industry Applications and Success Factors
Manufacturing Excellence Through RCM
Manufacturing operations represent the largest opportunity for reliability-centered maintenance implementation, with production equipment downtime costing $50,000 per hour on average. Successful manufacturing RCM programs focus on preserving production capability while optimizing maintenance resource allocation.
Critical manufacturing applications include:
Production line optimization through systematic analysis of bottleneck equipment, quality-critical processes, and high-availability requirements. RCM methodology helps prioritize maintenance efforts on equipment with highest production impact.
Quality system reliability ensuring consistent product quality through reliability analysis of measurement systems, environmental controls, and process stability equipment. Failure consequence analysis drives appropriate maintenance strategies for quality-critical functions.
Safety system assurance maintaining protective device reliability through systematic analysis of emergency stops, interlocks, guards, and monitoring systems. Hidden failure analysis ensures safety function availability when needed.
Energy efficiency optimization preserving equipment energy performance through condition monitoring and maintenance strategies that prevent efficiency degradation over time.
Aviation: RCM's Proven Foundation
Commercial aviation pioneered reliability-centered maintenance in the 1960s, achieving remarkable success in improving aircraft reliability while reducing maintenance costs. Modern aircraft achieve 99.5% dispatch reliability through systematic RCM implementation.
Aviation RCM achievements include:
- 25-35% maintenance cost reduction compared to traditional scheduled maintenance
- Improved safety performance through systematic failure consequence analysis
- Optimized maintenance planning based on actual reliability requirements rather than arbitrary time intervals
- Enhanced operational availability through condition-based maintenance strategies
The MSG-3 methodology used in commercial aviation demonstrates RCM effectiveness when properly implemented with appropriate technology support and organizational commitment.
Process Industries and Utilities
Process manufacturing, oil and gas, and utility operations benefit significantly from RCM implementation due to high consequence failures and complex system interactions. These industries typically achieve 15-30% maintenance cost reductions while improving reliability and safety performance.
Key success factors include:
- Systematic consequence analysis considering safety, environmental, and economic impacts
- Integration with process safety management ensuring maintenance strategies support overall risk management
- Technology-enabled condition monitoring providing data for predictive and condition-based maintenance
- Cross-functional team engagement including operations, maintenance, engineering, and safety personnel
Implementation Strategy and Best Practices
Phase 1: Preparation and Planning
Successful RCM implementation begins with comprehensive preparation addressing organizational readiness, scope definition, and resource allocation. Organizations must commit to systematic methodology rather than seeking quick fixes or partial implementations.
Critical preparation activities include:
Scope definition and prioritization focusing initial efforts on high-impact systems rather than attempting comprehensive facility coverage. Start with 3-5 critical systems that represent diverse failure consequences and maintenance challenges.
Team formation and training establishing cross-functional teams with operations, maintenance, engineering, and reliability expertise. Team members require training in RCM methodology, facilitation techniques, and decision-making processes.
Data collection and analysis gathering historical maintenance data, failure records, operational information, and existing documentation. AI-powered analysis can identify patterns and priorities before formal RCM analysis begins.
Technology platform selection choosing appropriate tools for analysis, documentation, and ongoing management. Modern platforms integrate RCM methodology with CMMS, condition monitoring, and analytics capabilities.
Phase 2: Systematic Analysis
RCM analysis follows the seven-question framework systematically for each selected system. Modern AI-enhanced approaches can accelerate analysis while maintaining methodology rigor and improving outcome quality.
Enhanced analysis techniques include:
AI-powered failure mode identification using machine learning algorithms to analyze maintenance history, sensor data, and operational patterns. This approach identifies failure modes that human analysis might miss while reducing analysis time requirements.
Dynamic consequence assessment leveraging real-time operational data to assess failure consequences based on current conditions rather than static assumptions. Production schedules, market conditions, and operational modes affect consequence severity.
Intelligent task selection using optimization algorithms to evaluate task effectiveness, cost considerations, and resource constraints simultaneously. This ensures selected maintenance strategies provide maximum reliability benefit within available resources.
Automated documentation generating RCM analysis documentation automatically while maintaining SAE JA1011 compliance. This reduces administrative burden while ensuring analysis quality and traceability.
Phase 3: Implementation and Optimization
Task implementation requires integration with existing maintenance systems, procedures, and organizational processes. Success depends on change management, training, and continuous improvement rather than simply adding new maintenance tasks.
Implementation best practices include:
Gradual rollout approach implementing RCM-derived tasks systematically while monitoring performance and adjusting based on results. Avoid overwhelming maintenance organizations with simultaneous changes across multiple systems.
Performance monitoring and feedback tracking reliability indicators, maintenance costs, and operational availability to validate RCM effectiveness. Use data to refine maintenance strategies and demonstrate program value.
Continuous optimization leveraging ongoing performance data to refine maintenance strategies, adjust task frequencies, and identify improvement opportunities. AI-powered systems can automatically optimize based on performance trends.
Organizational learning capturing lessons learned, best practices, and success factors for application to additional systems. Build internal capability rather than depending entirely on external facilitation.
Technology Integration and Digital Transformation
IoT and Condition Monitoring
Internet of Things (IoT) sensors provide the data foundation for modern reliability-centered maintenance implementation. Wireless sensor networks enable comprehensive equipment monitoring without prohibitive installation costs or operational disruption.
Advanced monitoring capabilities include:
Vibration analysis using tri-axial accelerometers to detect bearing wear, misalignment, imbalance, and other mechanical issues before functional failure occurs. Machine learning algorithms can identify developing problems and predict remaining useful life.
Thermal monitoring through infrared sensors and thermal imaging to detect electrical problems, insulation breakdown, and process temperature deviations. Continuous monitoring provides early warning of developing issues.
Performance monitoring tracking equipment efficiency, energy consumption, and operational parameters to identify degradation trends and optimize maintenance timing based on actual condition rather than calendar schedules.
Environmental monitoring measuring operating conditions like humidity, contamination, and ambient temperature that affect equipment reliability and maintenance requirements.
Artificial Intelligence and Machine Learning
AI algorithms enhance every aspect of reliability-centered maintenance from initial analysis through ongoing optimization. Machine learning provides capabilities impossible with traditional manual approaches while reducing resource requirements.
Key AI applications include:
Anomaly detection using unsupervised learning algorithms like isolation forests and one-class support vector machines to identify unusual patterns in sensor data, maintenance records, and operational parameters.
Predictive modeling leveraging supervised learning to predict equipment failures, remaining useful life, and optimal maintenance timing based on current conditions and historical patterns.
Optimization algorithms using reinforcement learning and particle swarm optimization to optimize maintenance schedules, resource allocation, and task sequencing for maximum reliability benefit.
Natural language processing analyzing maintenance work orders, inspection reports, and operational logs to extract insights and identify emerging issues that structured data analysis might miss.
Digital Twin Technology
Digital twins create virtual representations of physical assets that enable advanced simulation, analysis, and optimization capabilities for reliability-centered maintenance implementation.
Digital twin benefits include:
Failure simulation modeling various failure scenarios to understand consequences and test maintenance strategies without risking actual equipment or production disruption.
Maintenance optimization simulating different maintenance approaches to identify optimal strategies considering reliability requirements, resource constraints, and operational impacts.
Training and knowledge transfer providing realistic environments for maintenance training and procedure development without requiring access to actual equipment.
Continuous improvement comparing digital twin predictions with actual performance to refine models and improve maintenance strategy effectiveness over time.
Measuring Success: KPIs and ROI
Key Performance Indicators
Effective RCM implementation requires systematic measurement of reliability improvements, cost reductions, and operational benefits. Key performance indicators should align with organizational objectives while demonstrating maintenance strategy effectiveness.
Primary reliability metrics include:
Overall Equipment Effectiveness (OEE) measuring the percentage of planned production time that equipment operates effectively. World-class manufacturers achieve 85% OEE, while average performers operate at 60%. RCM implementation typically improves OEE by 15-25%.
Mean Time Between Failures (MTBF) indicating equipment reliability through average operational time between breakdowns. Increasing MTBF demonstrates improved maintenance effectiveness and equipment condition.
Mean Time to Repair (MTTR) measuring average repair duration from failure detection to equipment restoration. RCM-derived maintenance strategies often reduce MTTR through better failure prediction and preparation.
Planned vs. Unplanned Maintenance Ratio tracking the balance between scheduled and emergency maintenance work. Leading organizations maintain 80% planned and 20% unplanned maintenance ratios.
Financial Performance Measurement
Return on investment calculation for RCM implementation must consider both direct cost savings and operational benefits. Successful programs typically achieve 120-600% ROI within 2-5 years.
Cost reduction categories include:
Maintenance cost optimization through elimination of unnecessary tasks, optimization of task frequencies, and transition from time-based to condition-based strategies. Organizations typically achieve 22-40% maintenance cost reduction.
Inventory optimization reducing spare parts inventory requirements through better failure prediction and maintenance planning. RCM analysis often identifies unnecessary spare parts while ensuring critical item availability.
Downtime reduction preventing unplanned equipment failures and optimizing maintenance scheduling to minimize production impact. Each hour of prevented downtime can save $50,000-$100,000 in manufacturing operations.
Quality improvement maintaining consistent product quality through reliable equipment operation and process control. Quality improvements often exceed direct maintenance savings in total economic benefit.
Operational Benefits Quantification
Beyond direct financial returns, RCM implementation provides operational benefits that support long-term competitive advantage and organizational capability development.
Operational improvements include:
Increased equipment availability through systematic failure prevention and optimized maintenance scheduling. Availability improvements of 2-5% typically result from effective RCM implementation.
Enhanced safety performance through systematic analysis of safety-related failures and appropriate maintenance strategies for protective devices and safety systems.
Improved regulatory compliance ensuring maintenance strategies address environmental, safety, and quality requirements effectively while minimizing compliance costs.
Organizational learning developing internal capability for systematic reliability analysis and maintenance strategy development that applies across all facility operations.
Common Implementation Challenges and Solutions
Overcoming the 70% Failure Rate
Traditional RCM implementations fail primarily due to inadequate planning, unrealistic expectations, and insufficient organizational commitment. AI-powered approaches address these challenges while providing additional success factors.
Primary failure causes include:
Resource underestimation with organizations expecting quick results without investing adequate time, personnel, or technology resources. Successful implementations require 12-24 months for initial systems plus ongoing optimization effort.
Analysis paralysis where teams become overwhelmed by methodology complexity and produce extensive documentation without actionable maintenance strategies. Focus on decisions and actions rather than documentation volume.
Integration failures when RCM analysis results don't connect effectively with existing maintenance systems, procedures, and organizational processes. Plan integration from project initiation rather than treating it as implementation afterthought.
Cultural resistance from maintenance personnel, operations staff, or management who prefer familiar approaches over systematic methodology. Address concerns through training, communication, and demonstration of early wins.
Technology Adoption Strategies
Successful technology integration requires careful planning, user training, and change management rather than simply installing new systems and expecting immediate adoption.
Technology success factors include:
User-centered design selecting platforms that integrate naturally with existing workflows rather than requiring completely new processes. Maintenance personnel should experience technology as helpful rather than burdensome.
Gradual capability building implementing basic functionality first, then adding advanced features as users develop confidence and competence. Avoid overwhelming users with complex capabilities immediately.
Training and support providing comprehensive training on both RCM methodology and technology platforms. Ongoing support ensures users can leverage full system capabilities effectively.
Performance demonstration showing clear connections between technology use and improved outcomes. Users adopt new approaches when they see direct benefits to their work effectiveness.
Organizational Change Management
Cultural transformation from reactive to proactive maintenance requires systematic change management addressing beliefs, behaviors, and organizational systems.
Change management strategies include:
Leadership commitment with visible executive support for RCM implementation including resource allocation, priority setting, and performance recognition. Leadership behavior demonstrates organizational commitment.
Communication strategy explaining RCM benefits, implementation approach, and individual roles clearly and consistently. Address concerns and misconceptions directly rather than ignoring resistance.
Training and development building internal capability rather than depending entirely on external facilitation. Develop champion networks that can support ongoing implementation and optimization.
Recognition and rewards aligning performance measurement and incentive systems with RCM objectives. Recognize individuals and teams who contribute to reliability improvements and methodology adoption.
Future of Reliability-Centered Maintenance
Industry 4.0 Integration
Smart manufacturing technologies are creating unprecedented opportunities for reliability-centered maintenance enhancement through real-time data, advanced analytics, and autonomous decision-making capabilities.
Emerging technology applications include:
Autonomous maintenance systems that can execute routine maintenance tasks, perform inspections, and make basic repair decisions without human intervention. These systems free skilled personnel for complex analysis and strategic work.
Augmented reality maintenance support providing technicians with real-time guidance, documentation, and expert consultation during maintenance activities. AR technology improves maintenance quality while reducing training requirements.
Blockchain maintenance records ensuring tamper-proof documentation of maintenance activities, compliance status, and equipment history. This technology supports regulatory compliance and warranty management.
5G-enabled communication providing high-speed, low-latency connectivity for real-time monitoring, control, and coordination of maintenance activities across distributed facilities.
Predictive to Prescriptive Evolution
Next-generation RCM systems will evolve beyond predicting when maintenance is needed to automatically prescribing optimal maintenance strategies and executing approved activities autonomously.
Prescriptive maintenance capabilities include:
Automatic strategy optimization continuously adjusting maintenance approaches based on equipment performance, operational requirements, and resource availability without human intervention.
Dynamic task scheduling optimizing maintenance timing and resource allocation in real-time considering production schedules, weather conditions, personnel availability, and parts inventory.
Intelligent troubleshooting providing step-by-step diagnostic guidance and repair recommendations based on symptoms, equipment history, and successful resolution patterns.
Continuous learning automatically refining maintenance strategies, failure predictions, and optimization algorithms based on outcomes and changing conditions.
Sustainability and Environmental Integration
Environmental sustainability is becoming increasingly important in maintenance strategy development, with organizations seeking to minimize environmental impact while maintaining operational reliability.
Sustainable RCM approaches include:
Energy efficiency optimization maintaining equipment energy performance through condition monitoring and maintenance strategies that prevent efficiency degradation over time.
Waste reduction minimizing maintenance waste through precise planning, reusable materials, and circular economy principles in spare parts management.
Lifecycle optimization extending equipment useful life through appropriate maintenance strategies while planning for sustainable end-of-life management.
Carbon footprint reduction optimizing maintenance activities to minimize energy consumption, transportation requirements, and environmental impact.
Getting Started with Modern RCM
Assessment and Planning
Before beginning RCM implementation, organizations should assess current maintenance practices, reliability performance, and readiness for systematic methodology adoption. This assessment guides implementation strategy and resource allocation.
Initial assessment areas include:
Current maintenance strategy effectiveness analyzing reliability performance, maintenance costs, and organizational satisfaction with existing approaches. Identify specific pain points and improvement opportunities.
Organizational readiness evaluating leadership commitment, resource availability, technical capability, and cultural readiness for systematic methodology adoption.
Technology infrastructure assessing existing CMMS, condition monitoring, and data management capabilities. Identify gaps and upgrade requirements for effective RCM support.
Skills and training needs evaluating current team capabilities and identifying training requirements for successful RCM implementation and ongoing optimization.
Technology Platform Selection
Choosing appropriate technology for RCM implementation significantly impacts success probability and long-term effectiveness. Modern platforms should integrate methodology, analysis tools, and ongoing management capabilities.
Platform evaluation criteria include:
Methodology compliance ensuring SAE JA1011 standard compliance while providing efficient analysis tools and documentation capabilities.
Integration capabilities connecting with existing CMMS, condition monitoring, ERP, and other organizational systems seamlessly.
AI and analytics providing machine learning algorithms, predictive modeling, and optimization capabilities that enhance traditional RCM methodology.
User experience offering intuitive interfaces that support adoption by maintenance personnel, engineers, and management without extensive training requirements.
Scalability and flexibility supporting expansion from initial pilot implementation to facility-wide deployment while adapting to changing organizational needs.
Implementation Roadmap
Successful RCM implementation follows a systematic roadmap that builds capability gradually while delivering measurable results throughout the process.
Recommended implementation phases:
Phase 1 (Months 1-3): Foundation Building
- Team formation and initial training
- Technology platform selection and setup
- Pilot system selection and data collection
- Baseline performance measurement
Phase 2 (Months 4-9): Pilot Implementation
- Complete RCM analysis for pilot systems
- Develop and implement maintenance strategies
- Monitor performance and adjust approaches
- Document lessons learned and best practices
Phase 3 (Months 10-18): Expansion and Optimization
- Apply methodology to additional systems
- Optimize technology platform utilization
- Develop internal facilitation capability
- Establish continuous improvement processes
Phase 4 (Months 19+): Ongoing Excellence
- Facility-wide RCM implementation
- Advanced analytics and AI utilization
- Cross-facility knowledge sharing
- Continuous strategy optimization
Conclusion
Reliability-centered maintenance represents the most systematic and effective approach to maintenance strategy development, but traditional implementation challenges have limited its widespread adoption. Artificial intelligence and digital technologies are revolutionizing RCM implementation, making it more accessible, effective, and valuable for organizations of all sizes.
The key to RCM success lies in combining proven methodology with modern technology platforms that address traditional limitations while providing enhanced capabilities. Organizations that embrace AI-powered RCM approaches will achieve superior reliability outcomes while reducing implementation complexity and resource requirements.
Factory AI's intelligent maintenance platform transforms traditional RCM implementation through automated analysis, real-time optimization, and continuous learning capabilities. By integrating artificial intelligence with established RCM methodology, organizations can achieve the reliability benefits that have made RCM the gold standard for maintenance strategy development.
The future belongs to organizations that leverage systematic approaches enhanced by intelligent technology. Start your RCM transformation today with platforms designed for modern manufacturing challenges and opportunities.
Ready to transform your maintenance strategy with AI-powered reliability-centered maintenance? Contact Factory AI to discover how intelligent automation can revolutionize your reliability outcomes while delivering measurable ROI.
Recommended Resources
Standards and Guidelines
- SAE JA1011: Evaluation Criteria for RCM Processes - Definitive RCM methodology standard
- ISO 55000 Asset Management - International asset management standards
- Society for Maintenance & Reliability Professionals (SMRP) - Professional development and certification
Educational Resources
- NIST Manufacturing Reliability Research - Government research on manufacturing reliability
- University of Maryland Reliability Engineering - Academic reliability programs
- Reliability Web - Industry knowledge and training resources
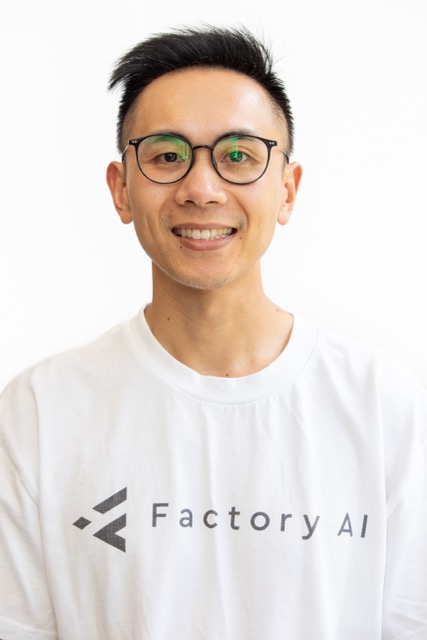