TRUSTED AND SUPPORTED BY
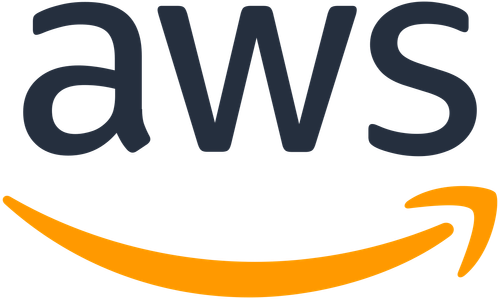
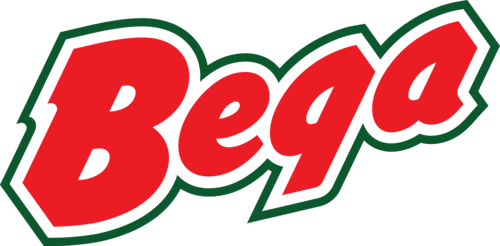
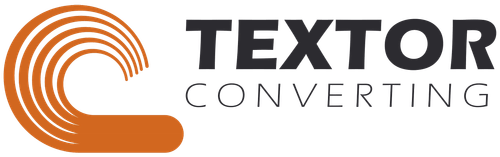
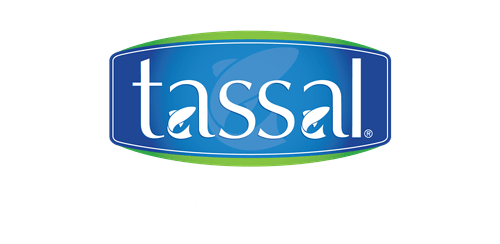
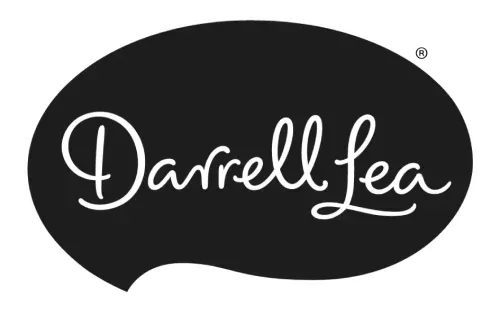
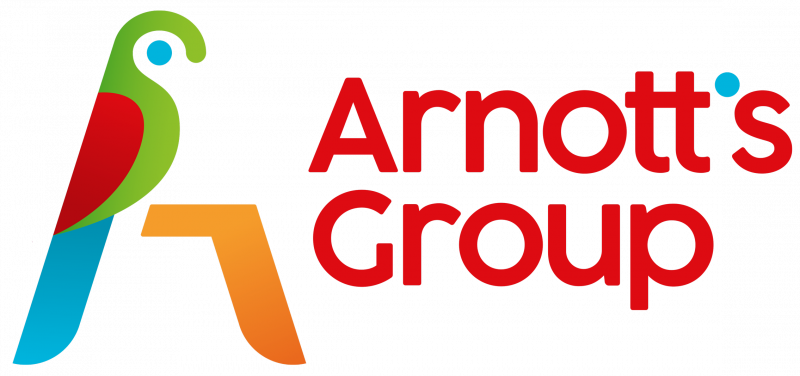
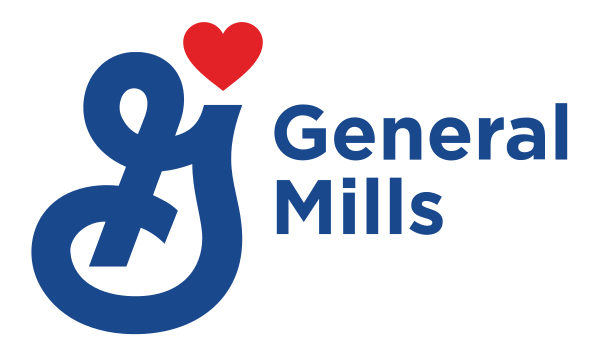
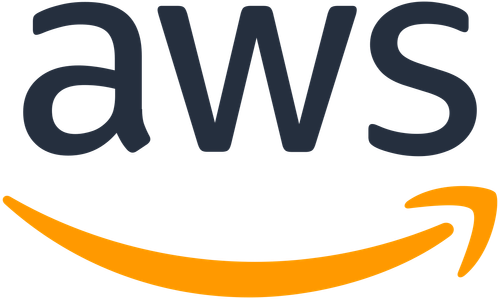
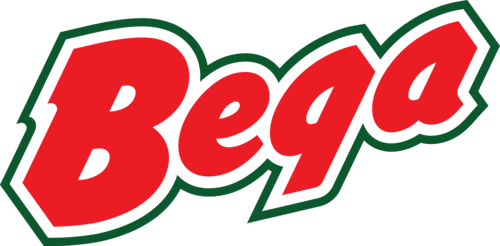
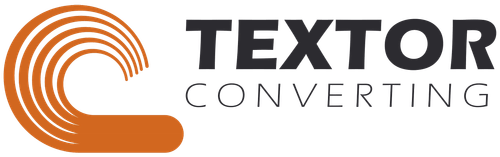
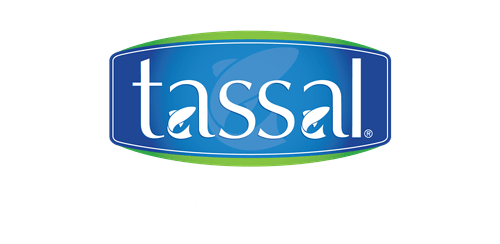
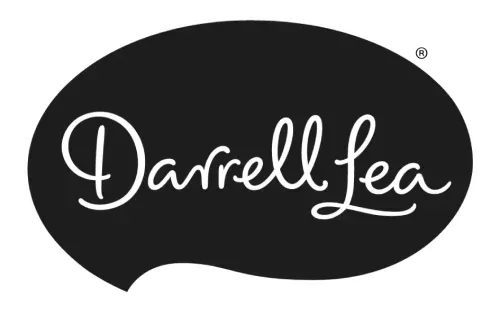
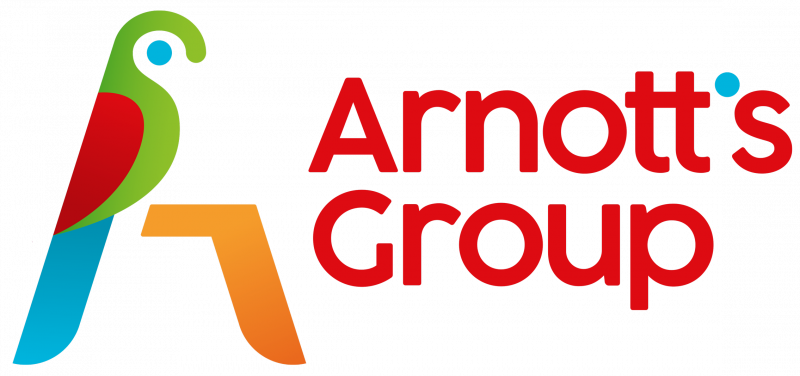
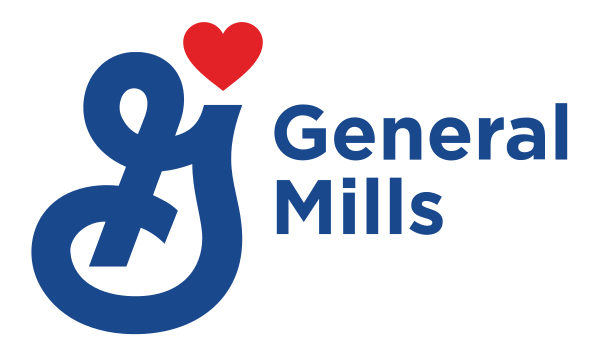
The Pitfalls of Inefficient Work Order Systems
Traditional work order software often focuses merely on tracking tasks rather than ensuring maintenance activities actually deliver value. This leads to wasted resources, recurring breakdowns, and frustrated teams.
Without a strategic RCM foundation, organizations struggle with an overload of non-value-adding preventive maintenance tasks and a reactive culture that addresses symptoms instead of root causes.
Excessive "just in case" PMs waste 30-50% of maintenance resources
Without clear linkage to failure modes, maintenance teams perform numerous unnecessary tasks that don't improve reliability.
Recurring defects indicate a focus on symptoms, not root causes
When work orders repeatedly address the same issues without resolving underlying problems, reliability suffers and costs compound.
Our Solution: AI-Enhanced, RCM-Driven Work Order Software
Our platform revolutionizes work order management by embedding RCM principles and leveraging powerful AI to create a proactive, data-driven maintenance ecosystem.
Foundation in Reliability Centered Maintenance
We start with the proven RCM methodology, focusing on preserving equipment function and identifying specific failure modes before creating work orders.
- Focus on preserving function, not just fixing parts
- Systematic identification of failure modes
- PMs only created for specific failure modes
AI-Powered Strategy & Content Generation
Our AI accelerates the RCM process, generating asset components, failure modes, maintenance strategies, and standardized procedures.
- AI-assisted asset component breakdown
- AI-generated failure modes and analysis
- AI-drafted maintenance procedures
Intelligent Work Order Creation
Work orders are automatically suggested based on RCM-derived maintenance strategies and condition monitoring alerts.
- Strategic work orders linked to failure modes
- Context-rich maintenance instructions
- Continuous improvement through feedback
Why Our Work Order Software Stands Out
RCM at its Core
Unlike systems that simply track tasks, we build your maintenance program on a foundation of reliability, ensuring every work order is strategically valuable.
Drastic Reduction in Non-Value PMs
Eliminate wasted effort by ensuring PMs are directly linked to probable failure modes, freeing up resources for more critical work.
Significant Defect Reduction
Proactively address the root causes of failures, leading to fewer breakdowns, increased uptime, and improved asset performance.
AI-Accelerated Implementation
Leverage AI to rapidly develop asset hierarchies, identify failure modes, and draft maintenance strategies and procedures, making RCM adoption faster and more efficient.
Data-Driven Optimization
Continuously improve your maintenance program based on real-world failure data and maintenance effectiveness.
Empowered Maintenance Teams
Provide your team with the tools and intelligence to move from a reactive to a proactive and strategic maintenance approach.
RCM-Driven Work Order Software in Action
Manufacturing Facility
Challenge:
A production line had excessive preventive maintenance tasks but still experienced frequent unplanned downtime due to equipment failures.
Our Approach:
Using our RCM-powered software, the company analyzed critical equipment like pumps and motors. The AI helped identify key failure modes and generated optimized PM schedules that focused specifically on these modes.
Before:
- 27 weekly PM tasks, many with unclear value
- Monthly line stoppages for "comprehensive" checks
- Still averaged 8 unplanned stops per quarter
After:
- Reduced to 15 targeted PM tasks
- Replacement of time-based PMs with condition monitoring
- Focus on critical lubrication points and wear patterns
- Unplanned stops reduced by 15%
Outcome:
The company reduced PM labor hours by 30% while simultaneously decreasing unplanned downtime. Maintenance resources were redirected to other value-adding activities, and overall equipment effectiveness improved by 6%.
Fleet Management
Challenge:
A logistics company was experiencing high maintenance costs and frequent roadside breakdowns despite an extensive preventive maintenance program.
Our Approach:
Our AI-assisted RCM analysis broke down vehicle systems, identified common failure modes (e.g., brake wear, DPF clogging), and suggested optimized inspection and replacement schedules based on usage patterns and failure data.
Before:
- Standard time-based service intervals regardless of usage
- Average of 3.8 roadside breakdowns per 10 vehicles quarterly
- All components serviced at same intervals
After:
- Customized service schedules based on actual usage profiles
- Predictive maintenance for critical components
- Focus on high-failure-rate items with minimal intervention on low-risk systems
- Roadside breakdowns reduced by 20%
Outcome:
The company reduced overall maintenance costs by 23% while significantly improving fleet reliability. Driver satisfaction increased due to fewer breakdowns, and on-time delivery performance improved by 8%.
The Technology: Smart, Not Just Automated
Our platform utilizes sophisticated AI and machine learning models trained on vast datasets of industrial equipment and maintenance practices to deliver intelligent work order software.
AI algorithms that understand equipment
Our models are trained on thousands of equipment types and failure patterns, enabling quick analysis of complex asset hierarchies.
Continuous learning and improvement
The system adapts over time, learning from maintenance outcomes to refine strategies and optimize work order effectiveness.
Intelligent work order creation
Work orders are automatically generated based on RCM analysis, condition monitoring data, and historical performance.
Transform Your Maintenance with Intelligent Work Orders
Move beyond simple task tracking. Implement work order software that actively improves reliability, reduces costs, and empowers your team.
Frequently Asked Questions
We've got everything you need to get started on your predictive maintenance journey.