Proactive Problem Solving: Intelligent Prescriptive Maintenance
Don't just predict failures—prevent them with actionable insights. Our prescriptive maintenance solution analyzes anomalies, contextualizes them with operational data, and delivers clear observations, probable causes, and specific recommendations.
TRUSTED AND SUPPORTED BY
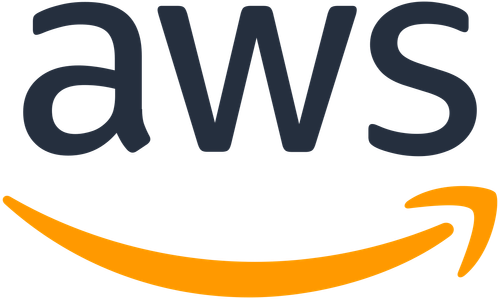
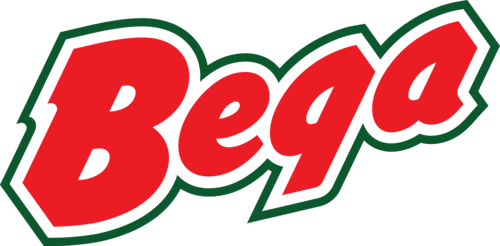
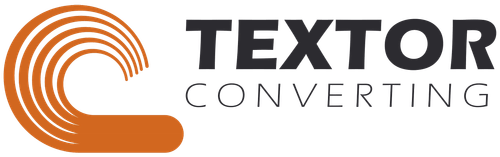
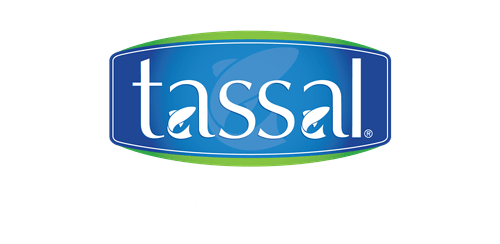
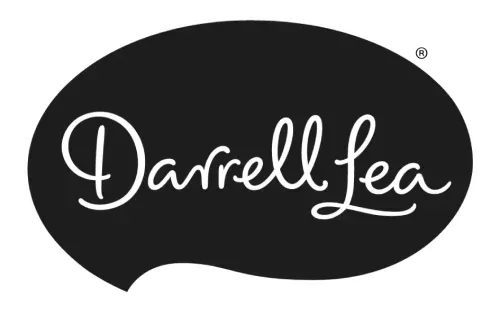
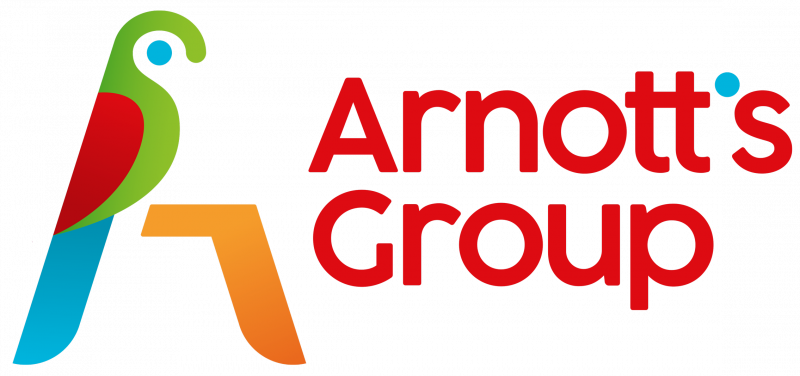
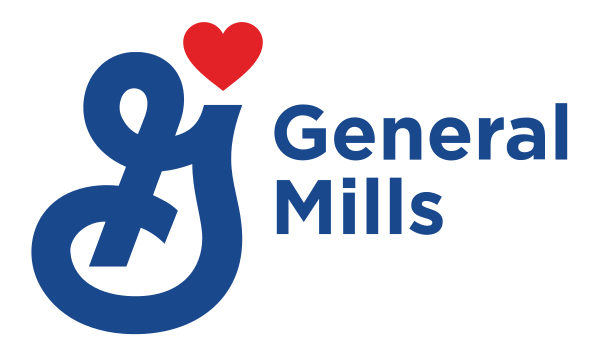
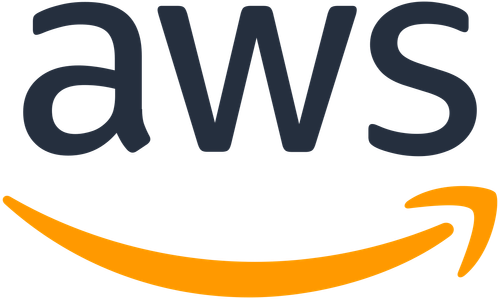
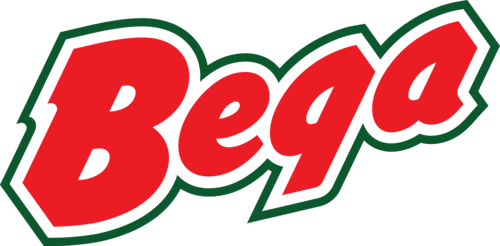
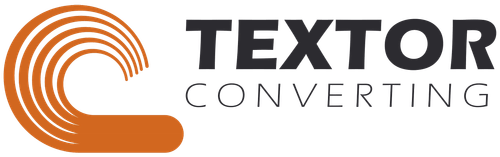
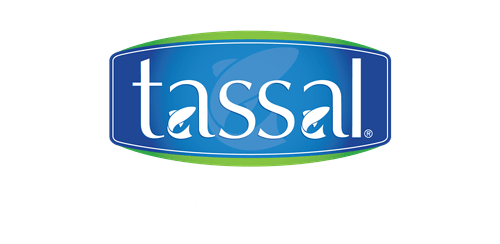
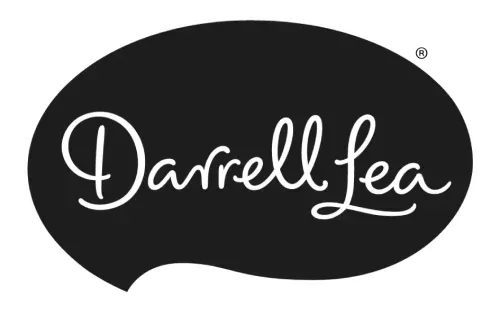
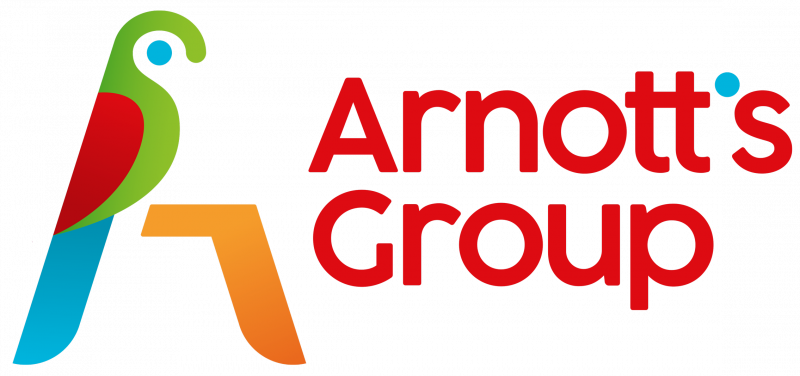
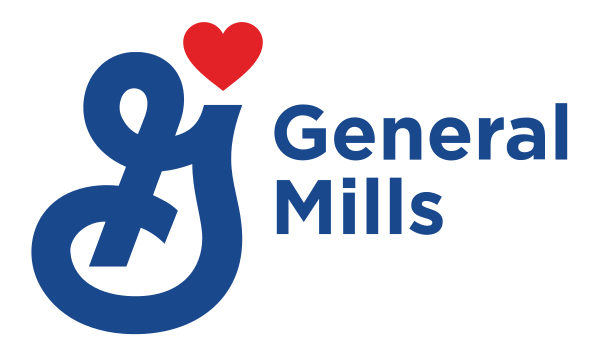
The Cost of Reactive Operations
Traditional maintenance approaches often leave businesses in a reactive state. Unforeseen equipment failures lead to costly unplanned downtime, inefficient use of resources, and missed opportunities for performance optimization.
Even basic predictive systems can raise alarms without offering clear guidance, leaving teams to decipher the next steps. This uncertainty translates to lost productivity and increased operational expenses.
Reactive maintenance costs 3-9x more than planned maintenance
Emergency repairs, expedited parts, overtime labor, and production losses dramatically increase costs when failures occur unexpectedly.
Predictive alerts without clear actions create analysis paralysis
When teams receive anomaly alerts without specific guidance on what to do, decisions are delayed and critical issues may go unaddressed.
Our Solution: Intelligent Prescriptive Maintenance in Action
Our innovative feature brings the power of prescriptive maintenance directly to your fingertips through a clear, structured approach that transforms complex data into actionable insights.
Automated Anomaly Detection
Sophisticated algorithms continuously monitor your operational data, identifying subtle deviations and patterns that signal potential issues before they escalate.
- Real-time monitoring of all critical parameters
- Detection weeks before traditional methods
- Pattern recognition across multiple data points
Deep Dive Analysis & Contextualization
Once an anomaly is flagged, our system delves deeper by analyzing the anomalous data in conjunction with a wide range of relevant operational data.
- Integration of historical performance data
- Correlation with maintenance logs and events
- Environmental and operational context inclusion
Actionable Insights Delivered
We distill complex findings into a straightforward format of observations, probability of cause, and specific recommendations.
- Clear observations of detected anomalies
- Ranked probable causes with confidence levels
- Specific, actionable recommendations
Why Our Prescriptive Maintenance Stands Out
Unparalleled Clarity
The "Observations, Probability of Cause, Recommendations" format eliminates guesswork. Your team receives clear directives, enabling faster, more confident decision-making.
True Contextual Intelligence
By integrating and analyzing data from across your operations, we provide insights that are far richer and more reliable than siloed anomaly alerts.
Reduced Downtime & Costs
Proactively addressing issues with specific guidance minimizes unplanned shutdowns and reduces the expenses associated with emergency repairs and lost production.
Optimized Performance
Beyond preventing failures, our prescriptive insights help you fine-tune processes and asset utilization for peak efficiency and extended equipment life.
Empowered Teams
We arm your operational and maintenance teams with the insights they need to shift from reactive firefighting to proactive, strategic problem-solving.
Continuous Learning
Our AI system continuously learns from outcomes, improving its recommendations over time and adapting to your specific operational patterns.
Real-World Prescriptive Maintenance in Action
Manufacturing Plant
Situation:
An unusual vibration pattern was detected in a critical motor that powers a main production line.
Our System's Response:
Observations:
Vibration amplitude increased by 32% over 72 hours, with frequency peaks at 85Hz and 170Hz. Recent increase in motor load detected (20% above baseline).
Probability of Cause:
75% - Bearing wear in drive-end position
15% - Misalignment at coupling
10% - Rotor imbalance
Recommendations:
1. Schedule bearing replacement during next planned maintenance window (5 days)
2. Reduce load by 15% if possible to extend bearing life
3. Prepare spare bearings and seals for quick replacement
Outcome:
Maintenance was performed during scheduled downtime. Inspection confirmed bearing damage. Replacement prevented an estimated 18 hours of unplanned downtime and $95,000 in production losses.
Energy Infrastructure
Situation:
A sensor network flagged a transformer with slightly elevated temperature readings at a critical substation.
Our System's Response:
Observations:
Top-oil temperature trending 8°C above normal over 14 days. Coincides with 12% increase in load and 5-day period of ambient temperatures exceeding 35°C.
Probability of Cause:
65% - Cooling system inefficiency (probable fouled radiator)
25% - Environmental stress during high ambient temperatures
10% - Insulation degradation beginning
Recommendations:
1. Inspect and clean radiator fins within 72 hours
2. Defer non-critical load increases until ambient temperatures drop
3. Verify oil pump operation and coolant flow rate
Outcome:
Inspection revealed partially clogged radiator fins. After cleaning, temperature returned to normal range. Prevented potential transformer failure that would have affected power delivery to 3,500 customers.
The Technology Behind the Intelligence
At the heart of our prescriptive maintenance feature are advanced Artificial Intelligence (AI) and Machine Learning (ML) algorithms that transform raw data into actionable intelligence.
Learning from vast data reserves
Our AI analyzes historical and real-time data to establish baselines and identify deviations that indicate potential issues.
Pattern recognition at scale
Advanced algorithms identify complex patterns and correlations invisible to the human eye, across thousands of data points.
Simulation and continuous improvement
Our system simulates potential outcomes of different actions and continuously refines its understanding based on feedback.
Take the Next Step to Proactive Operations
Stop reacting to problems and start prescribing solutions. Discover how our Intelligent Prescriptive Maintenance feature can transform your operations.
Frequently Asked Questions
We've got everything you need to get started on your predictive maintenance journey.