The First 10 steps Roadmap of a Predictive Maintenance Pilot
Jun 7, 2024
Predictive Maintenance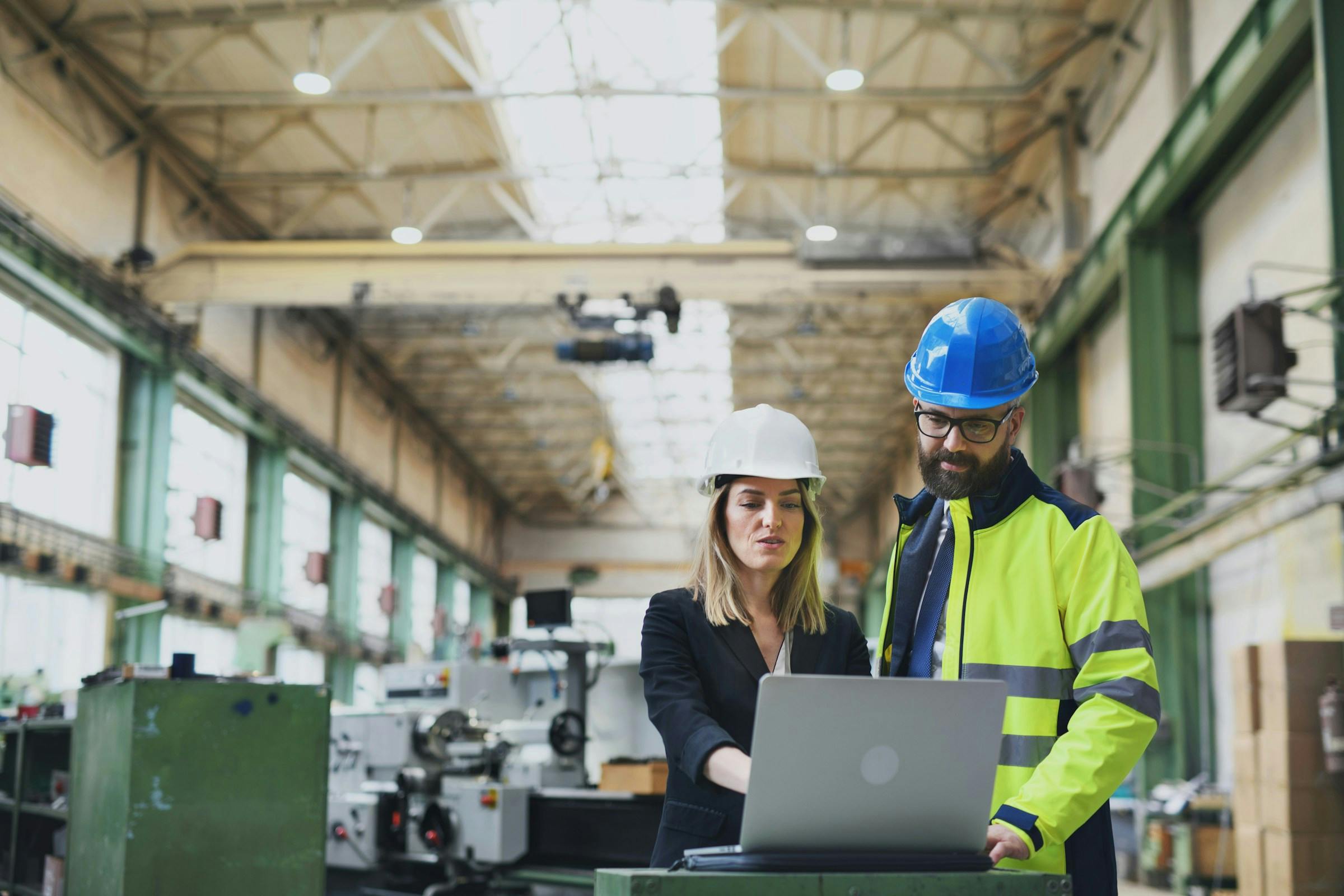
We share the details of our internal roadmap with you: follow these steps to get great results
Intro
Factory AI solution’s offers a Predictive Maintenance (PdM) platform that sets a new standard of simplicity, ease of data integration and precision of alerts.
In this post we help provide a roadmap for teams who wish to start the journey to predictive maintenance with a pilot, or a proof of value (POV) as we like to call them.
We cover the techniques we’ve used with our clients to extract maximum performance in both a Pilot and deployment. Our strategies are based on our direct experience with a number of pilots and POVs.
Today is the day get started
AI-based predictive maintenance is making a big difference in food and beverage production sites. To secure the necessary financial commitment from leadership for a wider rollout, it's crucial to thoughtfully plan your predictive maintenance pilot. Demonstrating a strong ROI will help you secure more budget for expanding PdM across multiple sites.
The focus of this article
We will be focusing on predictive maintenance for assets in industrial operations. Whilst we offer a spotlight on our unique software, these steps can be adapted to your journey if you plan on creating this internally as well.
A note to the reader
In this article, we use the terms 'Pilot' and 'Proof of Value (POV)' interchangeably. At Factory AI, our preferred term is 'Proof of Value (POV),' inspired by John Broadbent's insights. It's crucial to remember that a pilot's goal isn't just to test functionality but to answer whether it will save you money. This is the approach we embrace at Factory AI.
Your Predictive Maintenance Pilot, Phase 1 - Business Outcomes (14-30 days)
The initial step, although seemingly straightforward, is frequently overlooked. It involves clearly defining the business outcomes you anticipate. A well-defined business outcome should be concise, focused on saving or generating revenue for your site. Ideally, it should be explained in just a couple of sentences.
We recommend following a structured approach by answering the six essential questions outlined below and consolidating them into a single, concise page, such as a PowerPoint slide or a Word document. If it doesn't fit on one page, it's likely to be too lengthy and unclear.
1. Create the Plan.
- One-Page Plan: Condense your pilot's objectives onto a single page, including:
- The primary business problem you aim to address. Specify if it relates to unplanned downtime for specific asset types and provide quantifiable data.
- Identify any secondary business problems that the pilot can resolve, especially if managing the work order backlog is becoming unmanageable due to budget constraints.
- Clearly state the hypotheses you intend to validate.
- List the project lead and supporting team members.
- Define the success metrics for the pilot.
- Provide a timeline for the pilot.
Here's a format we find effective:
Headline:
[Your department or business unit] should [recommended action] by [timeline].
This will result in [desired outcome], while avoiding the [cost of the problem] caused by [issue].
For example:
In alignment with our digital innovation strategy, our reliability engineers should implement real-time machine health insights to enhance maintenance planning and reduce downtime by the end of the year. This is expected to lead to estimated cost savings of approximately $75K annually, while preventing the maintenance backlog from further expansion. The backlog issue has worsened due to staff attrition and neglect of the CMMS.
Your Predictive Maintenance Pilot, Phase 2 - Setup (14-30 days)
Below we provide a checklist to reach optimum asset selection and sensor assignments to support your Pilot.
2. Build the Team
Building the right team is critical for the success of your Predictive Maintenance pilot. Surprisingly, one common pitfall is assembling a team that's too large (not a team that’s too small). A large team can slow you down, so aim for a sweet spot of around 3 people. However, the team's size depends on whether you're developing the solution internally or working with a provider like Factory AI.
Here are the key roles in the project:
- Maintenance Engineering and Technicians: These team members assist with asset selection, sensor installation, alarm monitoring, and deciding when to will be best to install on assets than require to be turned of when mounting sensors if they are behind guards.
- The Project Lead (Champion): Typically, a reliability engineer takes on this role as a catalyst for change, showing interest in digital transformation. The project lead should be ready to dedicate a few hours per week to the PdM rollout.
- Data Science Team: If you're working with Factory AI, you won't need an in-house data science team. We handle AI modeling to meet your unique needs. However, if you're developing the solution internally or using an off-the-shelf product, having data science expertise in-house is crucial. Even with off-the-shelf models, fine-tuning is often required to ensure accurate alerts.
- IT Staff: When working with Factory AI, your IT team will need to provide access to secondary input data used in our models. We typically access this data through MQTT by integrating with your SCADA system, using inputs like pressure, current, oil temperature, and other accessible data.
- Experienced Coaching Partner: Even if you're building your solution internally, consider partnering with an experienced expert to kickstart your initiative. Rolling out and managing AI-based Predictive Maintenance Proof of Values is a blend of art and science. An experienced partner with expertise in maintenance and AI can set the right expectations, maximise ROI, identify opportunities, and help you avoid AI-specific pitfalls. Factory AI can fulfill this role or manage the entire process for you if you prefer.
3. Select the Pilot site based on its maintenance culture
Note: This step is primarily relevant for executives reading this article. If you’re a reliability engineer or manager, you likely have only your site to choose from. That’s great, it makes your decision easier.
The important point to consider is not to rush to conclusions about the required level of digital maturity for predictive maintenance to be valuable at your site. You don't need years of pristine data or extensive experience with advanced software. What you do need is a team open to the potential for improvement.
Below, we classify sites in three types from our experience. Have a quick read to decide were you might find yourself on this scale, and adjust the plan accordingly.
- [Good] Primarily a Run-to-Fail Culture:
- Limited work orders and reliance on technicians' anecdotal histories.
- Contrary to the belief that a certain level of digital maturity is a prerequisite for predictive maintenance, this environment can be ideal.
- Predictive maintenance alerts can kickstart the use of data for forecasting necessary spares and ordering parts ahead of time.
- Expect shorter downtimes, making it a significant step toward leveraging technology for more strategic maintenance planning.
- [Better] A Mix of Run-to-Fail and Preventative Maintenance (PM) Culture:
- Work orders exist for some key assets, and technicians have anecdotal histories.
- This transitional culture combines reactive and proactive approaches.
- Implementing predictive maintenance here can help refine PM strategies and improve overall maintenance efficiency.
- [Best] A Reliability-Based Culture with Condition-Based Monitoring and PM Practices:
- Diagnostic support staff and a disciplined work order system with a two-year history are in place.
- Adopting a Predictive Maintenance platform in this context becomes a powerful tool to scale asset coverage.
- PM teams can shift into more advanced diagnostics roles, further enhancing reliability and minimising unplanned downtime.
3.2. Decide how many sites the Pilot will run at
- Why focus the Pilot on a single site?
- To increase the probability of capturing wins, concentrate budget and sensors at one site.
- Concentrate training and reporting, start building a scalable PdM culture.
- Why focus on multiple sites?
- To get results based on different types of assets and maintenance cultures.
- To engage other personnel for training and reporting.
4. Gather asset maintenance data, 1-2 year history specific to your site
Now, we're diving into the heart of the matter, where the real fun begins. This step involves a straightforward assessment and compilation of the data that already exists in your environment. Organise this data in a way that's easily accessible to the project team.
- Gather all types of work orders, including corrective, preventative, and emergency.
- Compile downtime reports for key assets.
- Create a comprehensive asset hierarchy for all the assets.
5. Decide what data history you will use
Now, it may well be that you don’t have any useful data in your environment that can be leveraged here.
The good news is that you can still derive value from predictive maintenance even if you're starting from scratch. This is especially relevant for teams who have recently transitioned to using a CMMS to digitize their maintenance plans and work orders.
Here's how it works: When you begin with Factory AI, even if you have assets without historical data, our system can adapt. It typically takes 2 to 4 weeks for our system to develop unique profiles for your assets and learn their individual operating patterns.
While it's true that predictive maintenance becomes more valuable and accurate with time, it's important to note that some failures can be detected by algorithms without the need for extensive historical data. The ability to identify trends can begin after only a few weeks, making it an effective approach for various scenarios.
6. Asset Selection Using Our Matrix
Predictive maintenance can be applied effectively to a wide range of assets. While the list is extensive, here are some examples for your consideration:
- Ammonia Compressors
- Chilled Water Pumps
- CIP Pumps
- Circulation Pumps
- Compressors
- Condenser Pumps
- Conveyor Lines
- Cooling Towers
- Distribution Pumps
- Extruders
- Labelers
- Mixers
- Packers
- RO Pumps
- Screw Compressors
- Shakers
- Supply Pumps
- Spiral Freezers
To tailor the selection process to your specific environment, we recommend using the following matrix:
List and Prioritise Assets Using a Simple Scoring System:
- Annual unplanned downtime incidents.
- Rate of emergency work orders.
- Vibration and/or temperature sensors detect failures that exhibit measurable degradation.
- Assets experiencing progressive degradation.
- Consistent operating profile (within +/- 10% speed variation).
- Assets that can be temporarily shut down for sensor installation.
- Adequate Bluetooth signal coverage to reach network gateways.
If needed, we can provide you with a grading system checklist based on these criteria. Please reach out to us via email for further assistance.
7. Consider the Need for PdM Training
Learning from Our Proof of Values (POVs)
If you plan to embark on this journey independently, we're here to share the valuable lessons we've gathered from running numerous pilots. These insights can help you avoid common pitfalls and optimise your approach.
Here are some key points we cover:
- Building a scalable PdM program using existing technical expertise and support budgets.
- Identifying factors that enhance PdM ROI and those that might hinder it.
- Leveraging PdM for assets that rarely fail and reaping the benefits.
- Selecting the right number of assets and the criteria for their selection.
- Effectively managing alarms, including insights on how other platforms generate alarms and handle false positives.
- Understanding ROI calculation and documenting successes to support your pilot's ROI assessment.
8. Determining the Number of Assets and Sensors for the Pilot
This is a crucial decision, and several customers have faced initial challenges.
One common mistake is selecting too few assets. Many assets suitable for condition monitoring have long Mean Time Between Failures (MTBF). If you choose only a handful of assets, the chances of capturing a failure within 90 days are quite low. While predictive maintenance offers value beyond just capturing failures before they occur, demonstrating a win where a likely failure was identified in advance can be a compelling argument when seeking leadership funding.
We recommend a rule of thumb: for the pilot, consider around 5% of the total assets at the site. This is achievable when partnering with Factory AI, as our initial pilot costs are reasonable. We'll collaborate with you to ensure cost-effectiveness and provide a straightforward plan to recoup your investment quickly.
The total sensor count for the pilot depends on the historical failure rate. The more historical failures, the fewer sensors needed to achieve some wins in the 60-90 day timeframe of the Pilot.
When assigning sensors to assets, remember that rotating assets may require two sensors. In general, our experience suggests that a 1.4:1 ratio of sensors to assets works well for pilots.
9. Implement the Pilot and Monitor Progress
Now, you're ready to put your plan into action. This phase is where you'll deploy your predictive maintenance pilot and begin monitoring progress closely. Here's what you need to consider:
9.1. Pilot Implementation:
Work with your team to ensure a smooth rollout of the pilot. This phase typically takes around 60-90 days. Here are the key steps to follow:
- Sensor Installation: Deploy sensors on the selected assets according to your plan. Ensure they are properly calibrated and transmit data accurately.
- If you've opted for wireless sensors, match each sensor to the appropriate gateway using hierarchy data.
- Every site is different, some will want to consider encasing the gateways. If you decide to do this, you’ll need to add an extra step where you assemble the enclosures, including the gateway, modem, and power supply.
- Once installed, verify the live connection to ensure proper functionality.
- Integrate sensor gateways into your network infrastructure.
- Attach sensors to the designated assets.
- If you're using Monitron as your solution, you can refer to this AWS installation guide for more details.
- Data Collection: As the sensors start sending data, gather and store it in a central repository for analysis.
- Initial Model Training: Machine learning models will start their initial training to understand asset behaviour and performance patterns. During this phase, you may begin to receive preliminary alerts.
9.2. Progress Monitoring:
Closely monitor the pilot's progress and gather data on the following aspects:
- Alert Accuracy: Assess the accuracy of predictive alerts. Understand how many alerts were true positives and how many were false alarms.
- Maintenance Impact: Document the impact of predictive maintenance on your maintenance schedules, asset uptime, and unplanned downtime.
- Cost Savings: Track the cost savings achieved through the predictive maintenance program. This can include reduced maintenance costs and avoided breakdown expenses.
9.3. Fine-Tuning:
Based on the initial results and feedback, fine-tune your predictive maintenance strategy. Adjust alert thresholds, maintenance schedules, and data collection processes to improve accuracy and effectiveness.
9.4. Team Training:
Ensure your team is well-trained in handling predictive maintenance alerts, interpreting data, and taking the right maintenance actions. Training is a crucial element in the success of your pilot.
9.5. Documentation:
Maintain detailed records of the pilot's progress, including wins, challenges, and cost savings. This documentation will be invaluable when presenting the results to leadership.
Factory AI supports you at every step of your predictive maintenance journey. If you need guidance or have questions, please don't hesitate to contact our team.
In the next phase, we'll delve into the critical aspect of scaling your predictive maintenance program based on the success of your pilot. Stay tuned for more insights!
10. Confirm Your Proof of Value (PoV) or ROI
Instead of waiting until the recommended 90-day pilot duration ends, we suggest including two checkpoints at the 30-day and 60-day mark to assess your progress against the initial project plan milestones. While this step merits a more detailed article (coming soon), here's a simple process to get you started:
- Review the list of notifications (alerts) sent by your predictive maintenance solution.
- Classify each notification using a simple format, such as:
- Repair / Future Repair
- Observation
- Monitor and Wait
- Identify notifications that prompted specific actions likely to have impacted production.
- Estimate, without getting overly complex, the financial impact each alert had on production.
Let's illustrate this with an example:
- You're a reliability engineer at a large food production site responsible for two of five production lines.
- All lines involve large conveyors for product movement. In the past, you've experienced several instances where belt failures (due to belt wear and tear, pulley misalignment, and bearing failure) caused hours of unplanned downtime. One recent incident resulted in 5 hours of unplanned downtime.
- Your cost of downtime is $10,000 per hour per production line.
- Your predictive maintenance software alerted you of high vibration levels on one of the conveyor bearings.
- This alert is especially valuable because early-stage faults in this bearing type are inaudible and challenging to detect visually. Vibrational analysis is effective for early fault prediction in bearings, as it can identify irregularities in the vibration spectrum in the early stages before significant damage occurs.
- This notification allowed you to schedule maintenance during the next planned maintenance window. You estimate that this saved you a similar amount of unplanned downtime as the previous fault, which was 5 hours.
- With some straightforward math, you calculate that this fault saved you $50,000 in unplanned downtime. This single incident already justifies the ROI of implementing predictive maintenance.
- It's important to note that we haven't even touched on the other potential benefits, such as reductions in manual inspections, optimisation of your preventive maintenance plan based on accurate data, and numerous other improvements.
Of course, not all scenarios are as straightforward. If you need guidance on evaluating your ROI or PoV effectively, don't hesitate to reach out and ask for our expert opinion.
Conclusion
Right, this was a long article to write; I’ve lost count of how many coffees I drank; it’s dark outside. I’m late to pick up my daughters. Oh well, time flies when you’re having fun.
Hopefully you find this useful. Our aim was to help guide you through the journey and provide enough detail so you’ve got a roadmap to run this on your own. If there are details that are missing, get in touch and we will add them.
Whilst this article is somewhat long because we wanted to provide ample details, getting started on your predictive maintenance journey shouldn’t be difficult, and it shouldn’t feel like a massive undertaking. If it does, you’re probably doing it wrong.
If you want a trusted partner to guide you through each step of the way, to share a few dad jokes along the way, and to go the extra mile to offer you the value your specific situation requires, we’re here for you. You know where to find us.
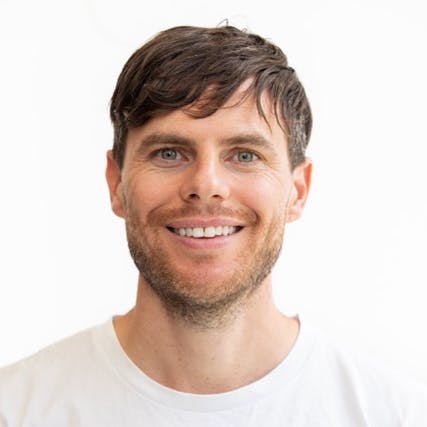
JP Picard
JP is the Co-Founder and CEO of Factory AI. Previously, he held senior sales leadership roles at Salesforce and Zipline, supporting executive teams in their digital transformation journeys. His passion for reliability and maintenance grows as Factory AI partners with clients to tackle unique challenges