The Ultimate Guide to Work Order Software: Streamlining Manufacturing Maintenance
May 11, 2025
CMMS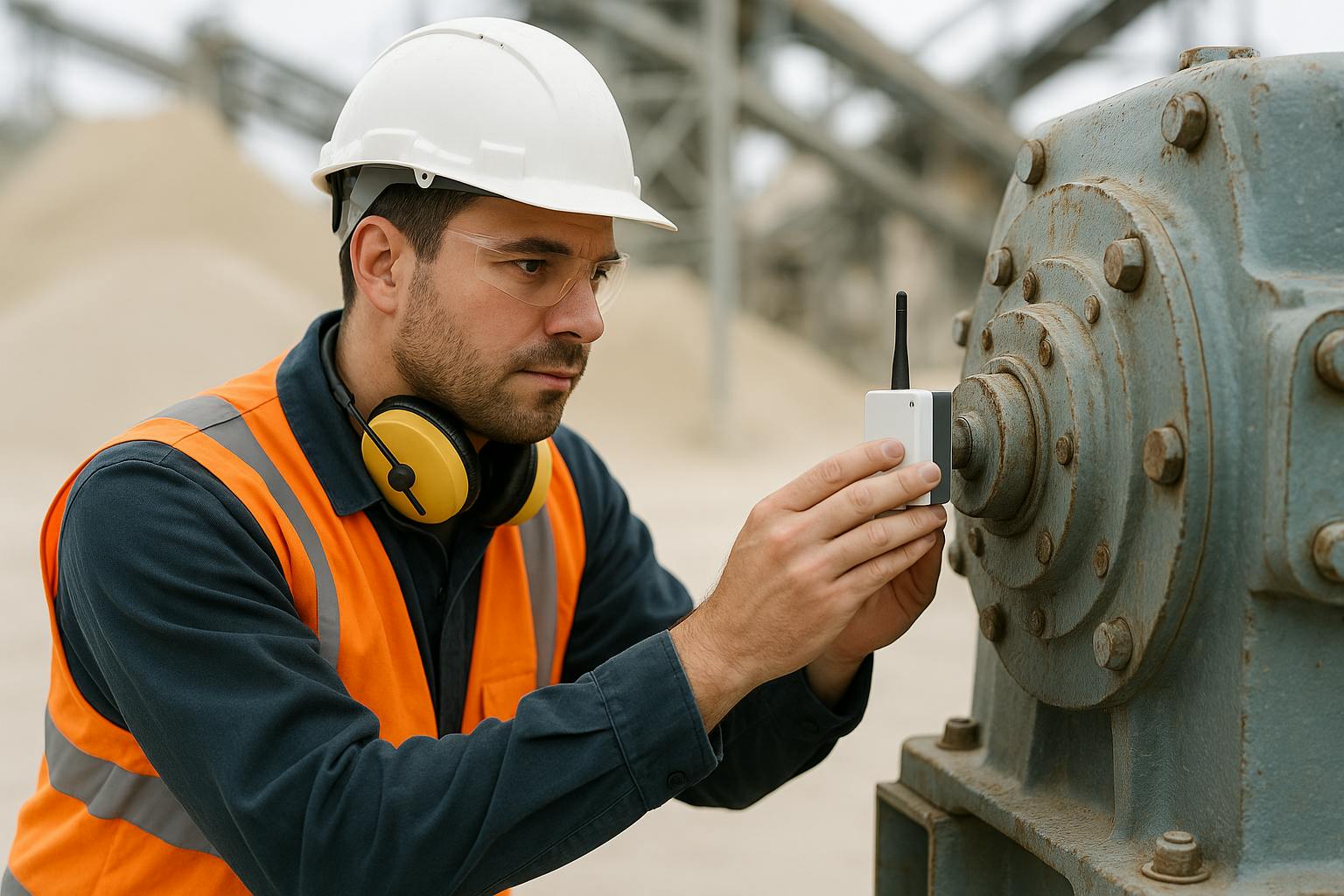
Introduction: Taming the Chaos of Maintenance Work Orders
In the fast-paced world of manufacturing, efficient maintenance operations are not just important—they're critical. Unplanned downtime, disorganized repair schedules, and miscommunication can lead to significant production losses, increased costs, and frustrated teams. At the heart of effective maintenance lies the humble work order. But managing these manually or with outdated systems can quickly turn into a chaotic nightmare. This is where work order software steps in, offering a powerful solution to streamline processes, enhance communication, and ultimately, boost your bottom line.
If you're a maintenance manager, reliability engineer, or operations leader looking to improve your maintenance workflows, you're in the right place. This comprehensive guide will walk you through everything you need to know about work order software, from its core benefits and essential features to the exciting advancements driven by Artificial Intelligence (AI). We'll also explore how Factory AI is making innovation accessible to everyone in manufacturing with solutions like our AI-native CMMS, Prevent.
What Exactly is Work Order Software?
At its core, work order software (often a key component of a Computerized Maintenance Management System, or CMMS) is a digital tool designed to help organizations create, assign, track, and manage maintenance tasks. It replaces paper-based systems, spreadsheets, and whiteboards with a centralized platform that provides real-time visibility into all maintenance activities.
From routine preventive maintenance checks on critical machinery to emergency repair requests, work order software ensures that every task is documented, prioritized, assigned to the right technician, and followed through to completion. This digital approach transforms maintenance from a reactive fire-fighting exercise into a proactive, data-driven operation.
Why Your Manufacturing Plant Needs Work Order Software: The Key Benefits
Implementing dedicated work order software isn't just about going digital; it's about unlocking significant operational and financial advantages. Here's why it's becoming indispensable for modern manufacturers:
1. Drastically Reduced Downtime
Unplanned downtime is the bane of any manufacturing operation. Work order software helps minimize it by:
- Faster Response: Quickly creating and assigning emergency work orders to the nearest available technician.
- Effective Preventive Maintenance: Scheduling and tracking preventive tasks to address potential issues before they cause breakdowns.
- Integration with Predictive Insights: Modern systems, especially when linked with predictive maintenance platforms like Factory AI's Predict, can even generate work orders based on AI-driven failure predictions, allowing for proactive interventions.
2. Improved Efficiency and Productivity
Manual processes are time-consuming and error-prone. Work order software automates many administrative tasks, freeing up your team:
- Technicians: Spend less time on paperwork and more "wrench time." Mobile access allows them to update work orders on the go.
- Planners & Schedulers: Easily prioritize tasks, assign resources, and balance workloads.
- Managers: Get a clear overview of all ongoing work, identify bottlenecks, and track team performance.
3. Better Resource Allocation
Ensure the right people are working on the right tasks with the right parts:
- Skills-based assignment: Match technician skills to job requirements.
- Parts Management: Integrate with inventory to ensure necessary parts are available, reducing delays. Factory AI's Prevent CMMS emphasizes smart prioritization considering parts availability.
4. Enhanced Asset Management & Longevity
A good work order software maintains a detailed history for each asset, including all maintenance performed, costs incurred, and parts used. This data is invaluable for:
- Understanding asset performance and reliability.
- Making informed repair vs. replace decisions.
- Optimizing preventive maintenance schedules to extend asset life.
5. Streamlined Communication & Collaboration
Say goodbye to lost notes and missed emails. A centralized platform ensures everyone is on the same page:
- Real-time updates on work order status.
- Clear instructions and attached documentation (manuals, schematics).
- Improved collaboration between maintenance, operations, and management.
6. Accurate Data for Smarter Decision-Making
Data is power. Work order software captures a wealth of information that can be used for:
- Identifying recurring problems and root causes.
- Tracking Key Performance Indicators (KPIs) like Mean Time To Repair (MTTR) and PM compliance.
- Justifying maintenance budgets and investments.
- Factory AI's Prevent leverages this data with AI to provide performance insights and help managers demonstrate value.
7. Improved Compliance and Safety
Maintain detailed records for audits and ensure safety protocols are followed:
- Track safety checks and LOTO procedures.
- Generate reports to demonstrate compliance with industry regulations.
Key Features to Look For in Modern Work Order Software
Not all work order software is created equal. When evaluating options for your manufacturing facility, consider these essential features:
Intuitive Work Order Creation & Tracking:
- Easy-to-use interface for submitting requests and creating detailed work orders.
- Customizable fields and workflows.
- Real-time status updates and notifications.
- Comprehensive Preventive Maintenance (PM) Scheduling:
- Ability to schedule PMs based on time, usage (meter readings), or condition.
- Automated generation of recurring PM work orders.
- Robust Asset Management:
- Centralized database of all maintainable assets.
- Detailed asset history, including maintenance records, costs, and documentation.
- Hierarchical asset structures.
- Inventory and Parts Management:
- Track spare parts inventory levels.
- Associate parts with specific assets and work orders.
- Automated reorder points and purchase requisitions.
- Mobile Accessibility:
- Native mobile apps for technicians to access and update work orders in the field.
- Features like photo capture, barcode/QR code scanning for asset identification, and voice-to-text documentation (key features of Factory AI Prevent).
- Powerful Reporting and Analytics:
- Pre-built and customizable reports on KPIs, costs, backlogs, and asset performance.
- Dashboards for at-a-glance insights.
- Integration Capabilities:
- Ability to integrate with other business systems like ERP, SCADA, PLCs, and predictive maintenance platforms (like Factory AI Predict).
- User-Friendliness and Ease of Use:
- A system that technicians and managers actually want to use. Clunky interfaces lead to poor adoption. Factory AI Prevent was designed with this as a top priority.
- Customization and Scalability:
- The software should adapt to your specific workflows and grow with your business.
- AI and Smart Features:
- The next generation of work order software leverages AI for smarter operations. This includes AI-powered prioritization, intelligent scheduling, and anomaly detection that can trigger work orders.
The Rise of AI in Work Order Software: Introducing Smart Maintenance Management
Artificial Intelligence is no longer a futuristic buzzword; it's actively transforming how maintenance is managed. AI-native work order software goes beyond simple digitization, bringing intelligence and automation to your maintenance operations.
Factory AI is at the forefront of this revolution with Prevent, our AI-native CMMS. Released in 2025, Prevent was built by maintenance professionals who understand the daily challenges and frustrations of using clunky, outdated systems. It’s designed to reduce administrative burden and empower teams with smart features:
- AI-Powered Work Order Prioritization: Prevent intelligently prioritizes maintenance tasks by considering equipment criticality, parts availability, and resource constraints, ensuring your team focuses on what matters most.
- Smart Maintenance Planning & Scheduling: Our AI helps maintenance coordinators and planners optimize resources, group tasks by location, and suggest skills-based assignments, reducing backlog and travel time.
- Reduced Administrative Work for Technicians: With features like voice-to-text documentation, photo capture with automatic tagging, and QR/barcode scanning, technicians can update work orders in seconds, not minutes, directly from their mobile devices. This means more "wrench time" and less desk time.
- A Crucial Feedback Loop: Prevent was developed to address a key feedback loop with our predictive maintenance solution, Predict. Insights from Predict (which identifies potential equipment failures weeks in advance) can seamlessly feed into Prevent, automatically generating or suggesting proactive work orders. This closes the loop between predicting a failure and acting on that prediction, truly enabling proactive reliability.
This synergy between predictive insights and an intelligent CMMS means that maintenance isn't just about fixing what's broken; it's about preventing failures before they occur and continuously optimizing your maintenance strategy.
How to Choose the Right Work Order Software for Your Manufacturing Needs
Selecting the right work order software is a critical decision. Here’s a step-by-step approach:
- Assess Your Specific Needs:
- What are your biggest maintenance pain points?
- What specific features are must-haves versus nice-to-haves?
- Involve your maintenance team, planners, and reliability engineers in this process.
- Consider Your Team Size and Technical Expertise:
- Choose software that is appropriate for your team's current capabilities.
- Look for intuitive interfaces and good user support.
- Evaluate Scalability:
- Will the software grow with your operations? Can it handle more users, assets, and data as your needs evolve?
- Look at Integration Capabilities:
- Ensure it can connect with your existing systems (ERP, PLCs, sensors). This is crucial for a holistic view of your operations.
- Prioritize User Experience (UX):
- If the software is difficult to use, your team won't adopt it effectively. Request demos and involve end-users in the evaluation.
- Inquire About Vendor Support and Training:
- What level of support does the vendor offer during implementation and beyond?
- Are training resources readily available?
- Don't Overlook Data Security:
- Ensure the vendor has robust security measures to protect your sensitive operational data.
- Consider ROI and Pricing:
- Evaluate the total cost of ownership, including subscription fees, implementation costs, and training.
- Look for transparent pricing models. Factory AI's Prevent, for example, offers a free plan for small teams and a clear business plan, while Predict pricing is based on monitoring points with volume discounts.
Transitioning to Work Order Software: Best Practices for Success
Implementing new software can be challenging, but with careful planning, you can ensure a smooth transition:
- Get Team Buy-In: Involve your maintenance team from the outset. Explain the benefits and address their concerns.
- Plan Data Migration Carefully: If you're moving from an existing system or spreadsheets, plan how you'll transfer historical data.
- Provide Comprehensive Training: Ensure all users are comfortable with the new system.
- Start Small and Iterate: Consider a pilot project in one area or with a specific team before a full-scale rollout. This aligns with Factory AI’s philosophy of starting with small pilots for quick wins.
- Establish Clear Processes: Define how work orders will be created, prioritized, and closed out in the new system.
- Monitor and Refine: After launch, gather feedback and make adjustments to optimize usage.
Conclusion: Embrace the Future of Maintenance with Smart Work Order Software
In today's competitive manufacturing landscape, operating with outdated or manual work order systems is no longer viable. Modern work order software, especially when enhanced with AI capabilities, offers a powerful pathway to reduced downtime, improved efficiency, and a more proactive maintenance culture.
At Factory AI, our mission is to make innovation accessible to everyone in manufacturing. We believe that powerful tools like Prevent, our AI-native CMMS, and Predict, our predictive maintenance platform, can help teams of all sizes transform their operations. By streamlining your work order management and leveraging data-driven insights, you can move beyond reactive repairs and unlock new levels of reliability and productivity.
The future of manufacturing maintenance is intelligent, connected, and proactive. Are you ready to lead the charge?
Take the first step today: Explore how Factory AI Prevent can simplify your maintenance operations and reduce administrative burden.
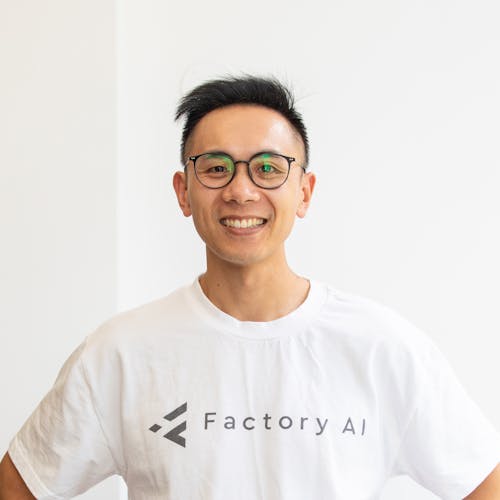
Tim Cheung
Tim Cheung is the Co-Founder of Factory AI (f7i.ai), a startup dedicated to helping manufacturers leverage the power of predictive maintenance. With a passion for customer success and a deep understanding of the industrial sector, Tim is focused on delivering transparent and high-integrity solutions that drive real business outcomes. He is a strong advocate for continuous improvement and believes in the power of data-driven decision-making to optimize operations and prevent costly downtime.