Unlocking the Promise: Why It's Time to Embrace Predictive Maintenance Software
Oct 24, 2023
Predictive Maintenance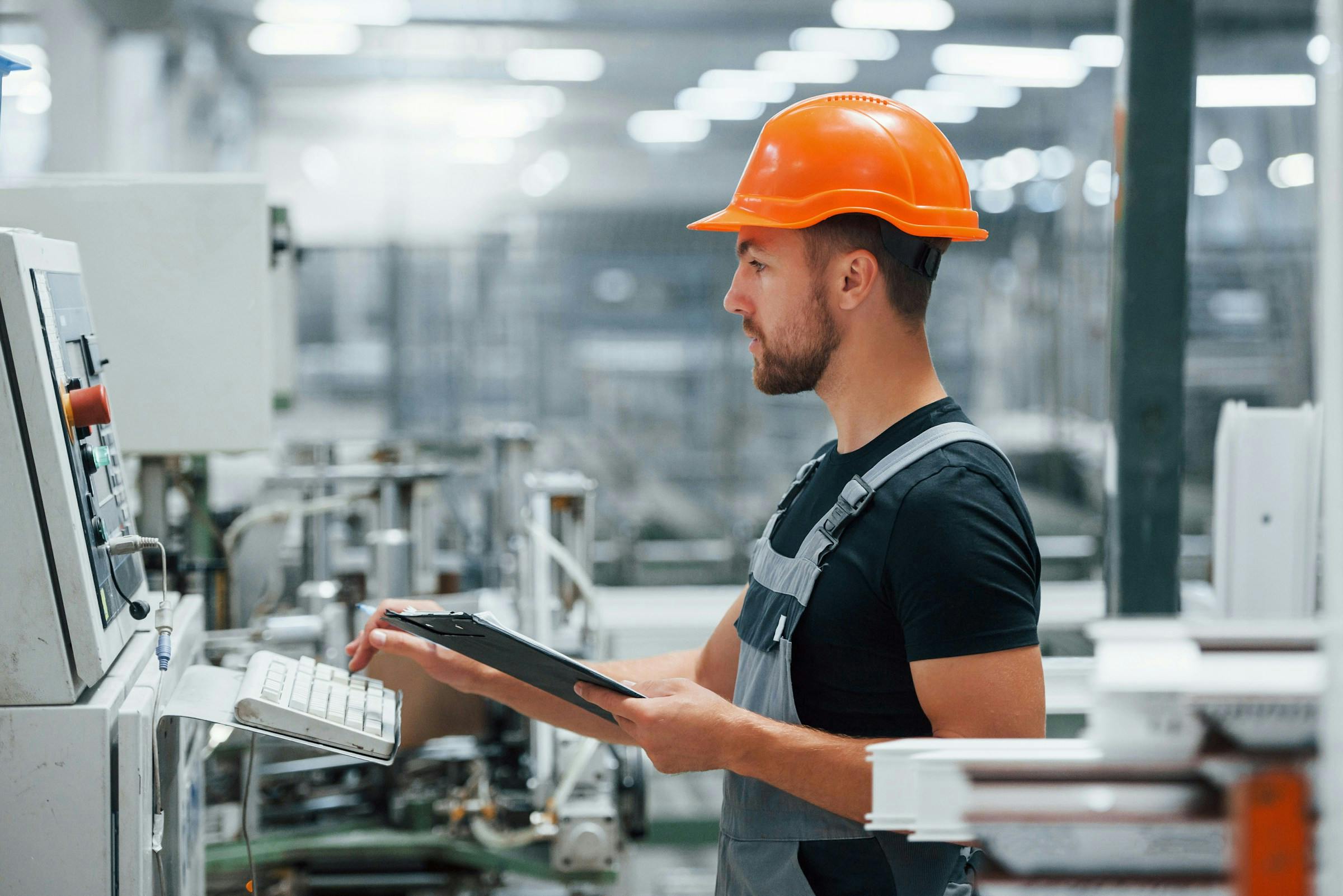
If you've attempted a smart condition monitoring project in the past without success, consider that recent advancements in AI and integration may make it worthwhile to give it another try.
Executive Summary
- Leadership teams acknowledge the increasing importance of data analytics and IIoT but may question its relevance for them. Why?
- Tesla's revenue quadrupled in the past four years, yet the pace of AI advancements might surpass even Tesla's remarkable growth.
- If you've attempted a smart condition monitoring project in the past without success, consider that recent advancements in AI and integration may make it worthwhile to give it another try.
Introduction
In the past year, we've engaged in several hundred conversations with leaders from manufacturing sites, focusing on reliability and maintenance.
While all acknowledge the growing importance of data analytics and the Industrial Internet of Things (IIoT) in the industry (as evidenced in Deloitte's 2023 manufacturing industry outlook report), a concerning majority express doubts about its applicability to their specific circumstances.
How do we make sense of this?
Upon further discussion, we often uncover stories of leadership teams who tried and encountered setbacks. A recurring theme is that the upfront effort, measured in terms of both time and cost, didn't seem to justify the expected benefits.
This article explores what’s changed in recent years, and why now might be a good time to circle back to predictive maintenance.
Hint: the answer lies in the significant advancements in the field of data analytics and AI
First, let’s start with a story
In 2019, Elon Musk was interviewed by Sandy Munro, a seasoned automotive industry veteran and an expert in vehicle 'tear-downs.'
During this candid conversation, Musk acknowledged Tesla's potential for improvement. He also pledged the company was committed to progress as it continued to mature.
The interviewer, Sandy Munro, formerly an industry expert working with renowned car manufacturers, operates a business dedicated to dissecting cars to uncover their manufacturing costs and construction methods (it’s pretty cool stuff).
The discussion with Musk began with Munro expressing some apprehension about Tesla's build quality, particularly in light of the backlash he had received from fervent Tesla enthusiasts.
As a specific example, Munro pointed out the varying panel gaps on different sides of a Tesla Model 3. In response, Musk openly admitted, 'I thought your criticisms were accurate’.
Elon revealed that when friends ask him when is the best time to buy a Tesla, he says “either buy it right at the beginning or when production reaches a steady state”.
Back to our Original Program
What does the story above have to do with past attempts at implementing a PdM approach?
Leaders we engage with often mention that they tried this years ago. When we delve into the specifics, '5+ years ago' is a common timeframe, and the memories of those experiences still linger.
There's a notable parallel here with Tesla's progress and the advancements in AI models over the last 5 years.
Credit where it's due, Elon Musk's Tesla has made remarkable strides. How else can we explain the company's revenue growth from $22 billion in 2019 (around the time of that interview) to nearly $100 billion in 2023?
While a near 4x improvement is undeniably impressive, it's possible that AI has advanced even further.
Although quantifying this advancement is challenging, it's our perspective.
Contextualising this improvement
This is incredibly relevant to predictive maintenance technology, namely smart-sensored condition monitoring given the value derives in surfacing signals from noise, and giving you higher quality warnings that come further ahead of time.
Let's put this improvement into context using a large dairy site in Australia as an example.
This facility boasts hundreds of assets, many equipped with smart sensors linked to the SCADA system. Alerts are displayed on screens throughout the plant.
A facility of this scale can generate over 10,000 signals from various sources. With extensive manual labor from an already stretched workforce, you might be able to monitor a few hundred of these signals using customised models to detect specific behaviours of interest.
This implies that 90% or more of these signals remain unmonitored. Just envision the numerous missed opportunities for receiving early warnings about deviations and other faults.
Many teams will go into predictive maintenance pilots with the objective to monitor every signal for any possible failure, at all times! However, given the immense scale we've just described, it's exceedingly challenging to anticipate every signal variance that might indicate a problem.
What's required is a more intelligent approach, and this is precisely what leads us to smart condition monitoring.
In essence, what we're saying here is that with the new, more capable tools, what was extremely difficult to achieve five years ago is now within reach.
What this means for you
What we're suggesting here is that it's possible you purchased your Tesla a bit too early, and indeed, you were the one to notice the gap between the panels.
If you didn't achieve the results you had hoped for in your initial venture into AI-based predictive maintenance, now might be the perfect moment to embark on this journey once more.
Take the time to apply the lessons you've learned from your previous experience and define the results you need to see this time to make it truly worthwhile.
If you're reading this and find this approach reasonable, we'd love to hear from you. Bring your story to the table, and let's discuss the possibilities.
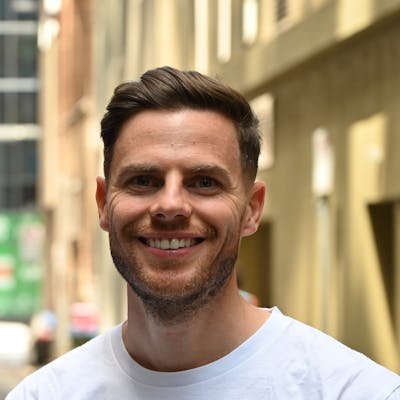
JP Picard
JP is the Co-Founder and CEO of Factory AI. Previously, he held senior sales leadership roles at Salesforce and Zipline, supporting executive teams in their digital transformation journeys. His passion for reliability and maintenance grows as Factory AI partners with clients to tackle unique challenges