Unmasking Idle Time: The Hidden Drain on Manufacturing Productivity and How to Stop It
May 12, 2025
Learn and be curious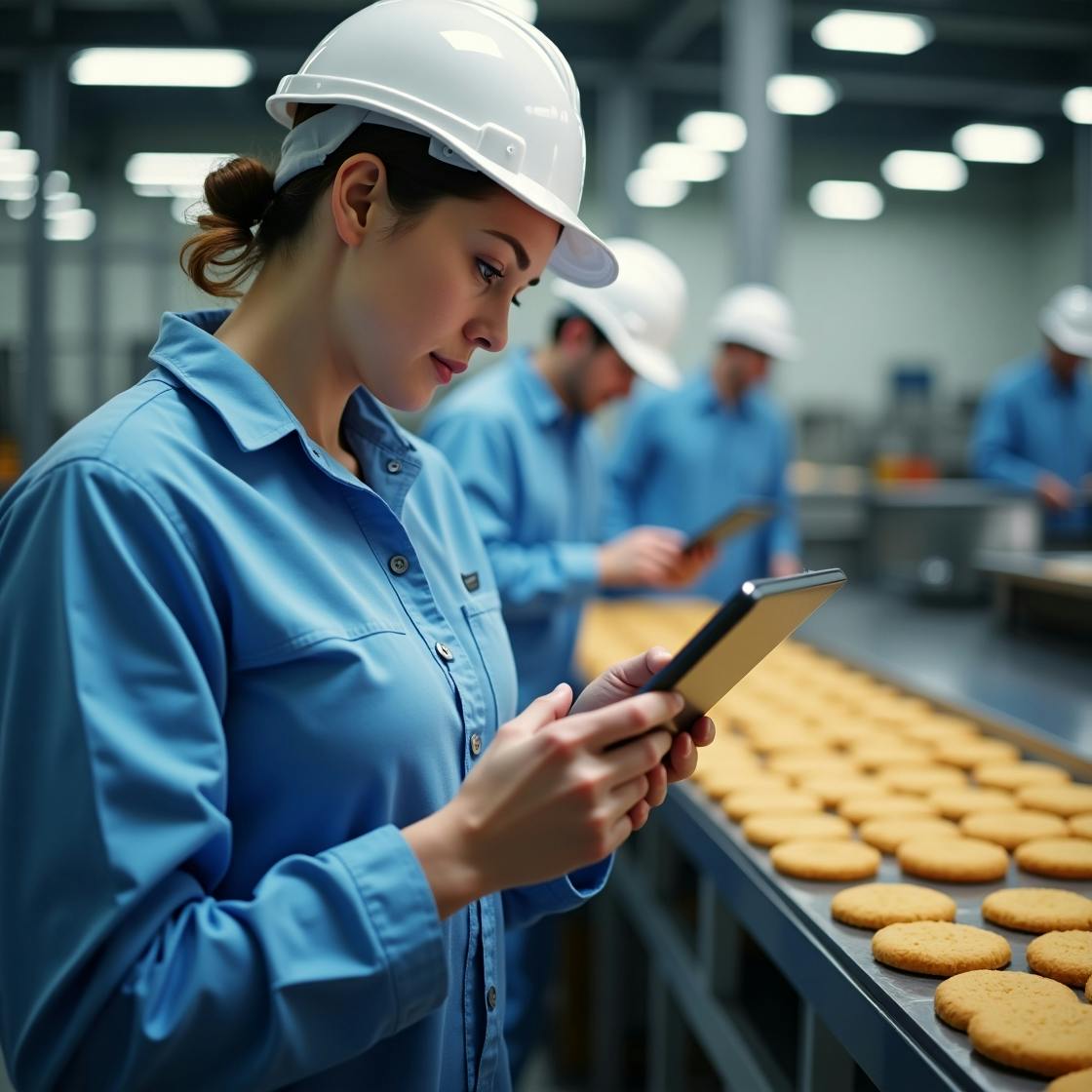
Introduction: The Silent Profit Killer in Your Factory
In the fast-paced world of manufacturing, every second counts. Efficiency and productivity are the cornerstones of success, yet a silent profit killer often lurks in the shadows: idle time. This is more than just a machine not running or an operator taking a break; it's a complex issue representing lost potential, wasted resources, and a direct hit to your bottom line. Understanding and actively combating idle time is no longer a luxury but a necessity for manufacturers aiming to stay competitive and innovative.
This comprehensive guide will delve into the intricacies of idle time in a manufacturing setting. We'll explore what it truly means, differentiate it from the more commonly understood "downtime," uncover its various causes, and most importantly, provide actionable strategies to significantly reduce it. We will also see how AI-native solutions, like those offered by Factory AI, are revolutionizing how manufacturers approach this pervasive challenge.
What Exactly is Idle Time in Manufacturing?
Idle time, often referred to as waiting time, is any period where machinery, equipment, or personnel are available and ready to work but are not engaged in productive tasks. Unlike downtime, where equipment is non-operational due to breakdowns or scheduled maintenance, idle time signifies a state of readiness without output. A machine might be perfectly functional but waiting for materials, or an operator might be on standby for the next production run.
This distinction is crucial. While downtime is about fixing what's broken, tackling idle time is about optimizing what's available. It’s about ensuring that your valuable resources – both human and mechanical – are utilized to their fullest potential when they are capable of working.
Idle Time vs. Downtime: A Critical Distinction
It's easy to confuse idle time with downtime, but they are fundamentally different:
- Idle Time: Equipment or personnel are available and capable of working but are not productive due to external factors (e.g., waiting for parts, upstream process delays, lack of operator).
- Downtime: Equipment is not available or not capable of working due to internal factors (e.g., breakdowns, scheduled maintenance, power outages).
While both result in a lack of production, their causes and solutions differ significantly. Recognizing this difference is the first step toward effectively addressing each. For instance, Factory AI's Predict solution focuses on preventing unplanned downtime by foreseeing equipment failures, while Prevent, our AI-native CMMS, helps streamline maintenance activities that, if poorly managed, could indirectly contribute to idle time by causing delays in returning equipment to a ready state.
The Pervasive Impact of Unchecked Idle Time
The consequences of excessive idle time ripple throughout a manufacturing operation, often with far-reaching financial and operational implications:
- Increased Operational Costs: Labor costs continue to accrue even when operators are idle. Similarly, machinery might consume energy even when not producing.
- Reduced Throughput & Output: Every minute of idle time is a minute of lost production, directly impacting your ability to meet demand and revenue targets.
- Lower Overall Equipment Effectiveness (OEE): Idle time negatively impacts the "Availability" component of OEE, a key metric for measuring manufacturing productivity.
- Missed Deadlines & Customer Dissatisfaction: Production delays due to idle time can lead to late shipments and unhappy customers.
- Wasted Capacity: Your facility has a certain production capacity. Idle time means this capacity is underutilized, representing a lost opportunity.
- Decreased Employee Morale: Constant waiting can be frustrating for operators who are ready and willing to work, potentially leading to disengagement.
Understanding these impacts underscores the urgency of identifying and mitigating idle time.
Common Culprits: What Causes Idle Time?
Identifying the root causes of idle time is essential for developing effective reduction strategies. Some common culprits include:
- Material Shortages/Delays: Equipment sits idle waiting for raw materials, components, or sub-assemblies.
- Upstream/Downstream Bottlenecks: A machine may be ready, but the preceding process hasn't supplied the input, or the subsequent process isn't ready to take the output.
- Poor Production Scheduling & Planning: Inefficient scheduling can lead to gaps between production runs or mismatched resource allocation.
- Equipment Changeovers: While necessary, lengthy or inefficient changeover processes between different products contribute significantly to idle time.
- Operator Unavailability: Lack of trained operators, improper shift planning, or unexpected absences can leave machinery unmanned.
- Lack of Work Orders or Instructions: Operators may be idle if they haven't received clear instructions or work orders for the next task.
- Quality Control Hold-Ups: Production might pause while waiting for quality checks or approvals.
- Inefficient Workflows: Poorly designed processes or facility layouts can create unnecessary waiting periods.
- Minor Stoppages: Frequent, short interruptions that may not be logged as downtime but collectively add up to significant idle time.
Effectively pinpointing these causes in your specific environment is crucial. This is where data collection and analysis, supported by tools like Factory AI's Prevent CMMS, become invaluable. By logging and categorizing sources of idle time, patterns can emerge, guiding targeted improvement efforts.
Strategies to Minimize Idle Time and Boost Efficiency
Reducing idle time requires a multi-faceted approach, integrating people, processes, and technology. Here are key strategies:
1. Optimize Production Planning and Scheduling
- Advanced Planning Systems (APS): Implement APS tools that can create optimized schedules, considering material availability, resource capacity, and order priorities.
- Just-In-Time (JIT) Principles: Minimize inventory holding and ensure materials arrive just as they are needed for production, reducing waiting for parts.
- Clear Communication: Ensure seamless communication between planning departments, shop floor supervisors, and operators regarding schedules and any changes.
2. Streamline Workflow and Process Efficiency
- Value Stream Mapping (VSM): Identify and eliminate non-value-added activities (including waiting) in your processes.
- Standardized Work Procedures: Develop and implement clear, standardized operating procedures for all tasks to minimize confusion and delays.
- SMED (Single-Minute Exchange of Die): Implement SMED techniques to drastically reduce equipment changeover times.
- Improved Facility Layout: Optimize the physical layout of your plant to reduce material movement and waiting times between process steps.
3. Enhance Workforce Management and Training
- Cross-Training Operators: Train operators on multiple machines or tasks to increase flexibility and reduce reliance on specific individuals.
- Effective Shift Handovers: Implement structured shift handover processes to ensure a smooth transition of information and responsibilities, minimizing startup delays for the next shift.
- Empower Operators: Provide operators with the information and authority to address minor issues that could lead to idle time.
4. Leverage Technology for Real-Time Monitoring and Control
This is where AI-native solutions can make a transformative impact.
- Implement a Modern CMMS: A robust Computerized Maintenance Management System (CMMS) like Factory AI's Prevent is crucial.
- Prevent can help track idle time by allowing maintenance planners and technicians to log reasons for delays more accurately when equipment is available but not running due to maintenance-related coordination (e.g., waiting for a specific craft, permit, or part that was supposed to be ready).
- By streamlining maintenance planning and execution, Prevent ensures that when scheduled maintenance is completed, equipment doesn't sit idle waiting for final checks or handovers. This addresses the feedback loop problem that inspired Prevent’s creation.
- Reliability engineers and maintenance managers can use Prevent's analytics to identify recurring causes of such maintenance-related idle time and optimize their processes.
- Utilize Predictive Maintenance (PdM): While primarily aimed at reducing downtime, solutions like Factory AI's Predict also play a role in minimizing idle time.
- By predicting potential equipment failures, Predict allows maintenance to be scheduled proactively and efficiently. This prevents unexpected breakdowns that can cause upstream or downstream processes to become idle.
- Reliability engineers and maintenance leaders using Predict can better anticipate when a machine might need attention, allowing for smoother integration of maintenance into production schedules, thus reducing periods where other machines or personnel are idly waiting.
- Real-Time Performance Monitoring (MES/IIoT): Manufacturing Execution Systems (MES) and Industrial Internet of Things (IIoT) platforms can provide real-time visibility into machine status, including idle time. This allows for immediate identification and response to idle events.
5. Foster a Culture of Continuous Improvement
- Data-Driven Decisions: Regularly collect and analyze data on idle time, its causes, and its impact. Use this data to prioritize improvement efforts.
- Engage Employees: Involve shop floor personnel in identifying causes of idle time and brainstorming solutions. They often have the best insights into day-to-day operational friction.
- Regular Reviews: Conduct periodic reviews of your idle time reduction initiatives to assess their effectiveness and make adjustments as needed.
Case Study Snippet: Reducing Changeover Idle Time with AI-Assisted Scheduling
A mid-sized automotive parts manufacturer was struggling with significant idle time on their CNC machining line, primarily due to lengthy and unpredictable changeovers. By implementing an AI-assisted scheduling module integrated with their CMMS (similar to how Prevent could be enhanced), they gained better insights into optimal changeover sequencing. The system analyzed historical changeover data and upcoming orders to suggest grouping similar jobs, minimizing the extent of re-tooling needed. Furthermore, Prevent helped ensure that all necessary tools and personnel for the changeover were ready before the current job finished, drastically cutting down the "waiting for resources" component of idle time. This led to a 15% reduction in overall idle time on that line within three months.
Conclusion: Turning Idle Time into Productive Time
Idle time is a multifaceted challenge in manufacturing, but it's not an insurmountable one. By understanding its definition, impact, and causes, and by strategically implementing a combination of optimized processes, skilled workforce management, and powerful technologies, manufacturers can significantly reduce this drain on productivity.
Factory AI is committed to making innovation accessible to everyone in manufacturing. Our solutions, Predict and Prevent, are designed to empower reliability engineers, maintenance planners, managers, technicians, and operations leaders to tackle not just equipment downtime but also the pervasive issue of idle time. By transforming your approach to maintenance and operational efficiency with AI-native tools, you can unlock hidden capacity, reduce costs, and pave the way for a more productive and profitable future.
Ready to stop watching your profits diminish during periods of inactivity? Explore how Factory AI's Predict solution can help you anticipate issues and how Prevent, our AI-native CMMS, can streamline your maintenance operations to minimize idle time. Contact us to get started!
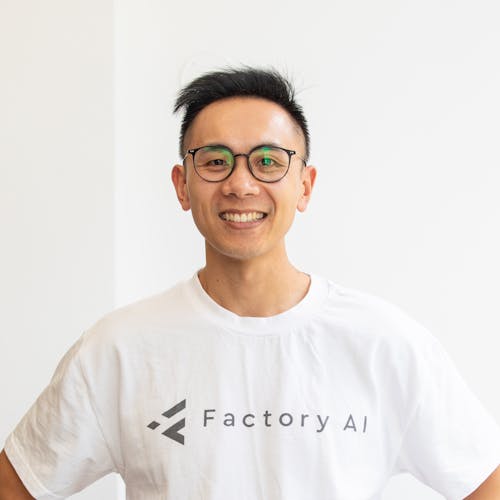
Tim Cheung
Tim Cheung is the Co-Founder of Factory AI, a startup dedicated to helping manufacturers leverage the power of predictive maintenance. With a passion for customer success and a deep understanding of the industrial sector, Tim is focused on delivering transparent and high-integrity solutions that drive real business outcomes. He is a strong advocate for continuous improvement and believes in the power of data-driven decision-making to optimize operations and prevent costly downtime.