Warren’s 5/25 rule applied to Maintenance and Reliability
Jun 7, 2024
Predictive Maintenance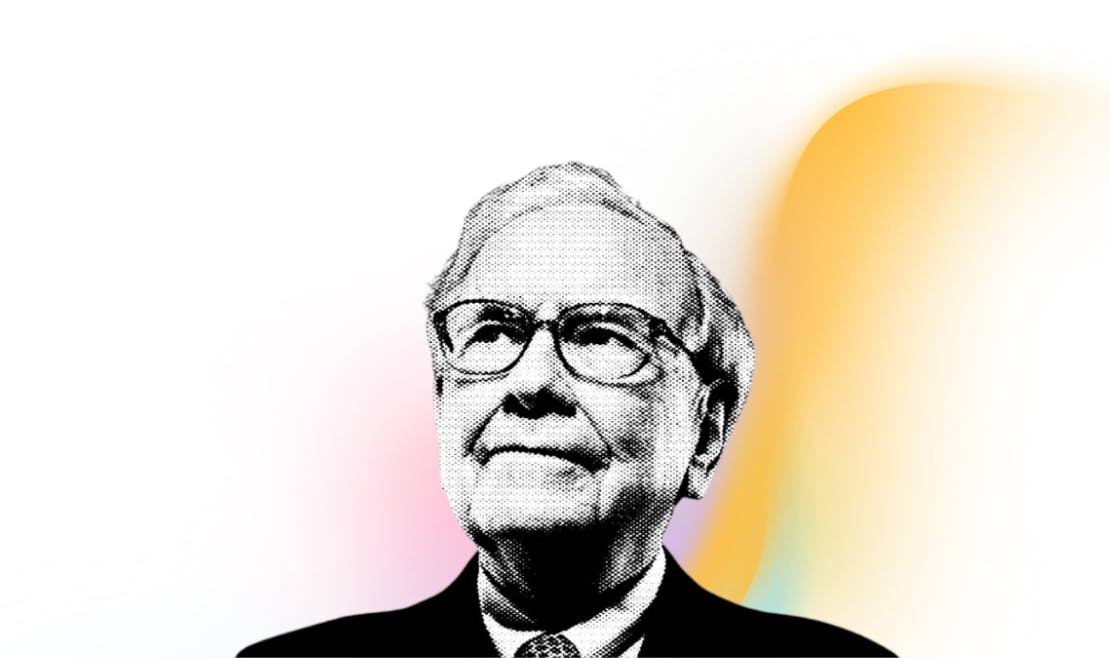
Warren's 5/25 rule underscores focused prioritisation of your top 5 goals for success. This article discusses applications to reliability engineering.
Warren’s 5/25 rule
A number of years ago, Warren had a conversation with his personal airplane pilot Mike Flint.
Mike had been serving Warren for a decade at this point, and Warren thought it was a good time to get him to write down his 25 important goals.
Once Flint presented Buffett with his list of 25 major life goals, Buffett asked him to prioritise and circle his 5 most important goals.
Then, Buffet asked what Mike was planning to do with his remaining 20 goals.
Flint responded that since all these were important to him, he would spend time on the remaining 20 items when he was not working on his main 5 goals.
To this, Buffet responded:
"Everything you didn’t circle just became your Avoid-At-All-Cost list. These things get no attention from you until you’ve succeeded with your top 5.”
That’s the power of selective focus and this rule is known as 5/25 Rule.
Spending time on secondary priorities is often the reason teams end up with 20 half-finished projects instead of focusing strongly on their top 5 priorities.
The rule’s application to reliability and maintenance
This principle behind this is that focus is the key to success.
Robert Kiyosaki, coined an interesting acronym for focus:
F- Follow
O- One
C- Course
U- Until
S- Successful
Warren’s strategy, to prioritise the most important goals and “avoid at all cost” the trivial many, reminds us that success is as much what you don’t do, as it is what you do.
A reliability leader can accomplish great change if they pick 3-5 areas to improve. Any more than 5 (at any one time) tends to be too difficult.
Delving deeply into a few select areas and aligning across the organisation is the starting point for making progress toward greatness.
Each year, the focus can change to a new 3-5, but we need to use caution to ensure we are not jumping to new targets without locking in hard-fought gains.
Our experience of working with reliability leaders tells us that when they reflect on previous failures, too many mention a focus on 20+ KPIs and make slow progress on them all.
This behaviour often stems from the desire to please senior leadership and the aspiration to make a quick, significant impact. While having more KPIs might seem like a good defence in some cases, the reality differs from the theory.
How this applied to Factory AI working with you
Factory AI's unique approach to predictive maintenance won't be suitable for everyone. With our mission to make innovation accessible to all manufacturers, we understand that innovation needs to occur at the right time and with the appropriate level of readiness.
The challenge of reducing unplanned downtime and optimising asset performance must be one of the current top 3 to 5 priorities.
If you've included in your plan this year the goal of significantly reducing failures in a key set of assets, we might be able to assist you. There’s no sales pitch when you speak with us; we’ll be honest about what we can do and what we can’t.
Here’s to solving problems!
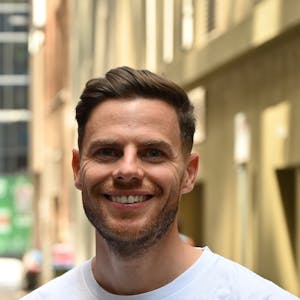
JP Picard
JP is the Co-Founder and CEO of Factory AI. Previously, he held senior sales leadership roles at Salesforce and Zipline, supporting executive teams in their digital transformation journeys. His passion for reliability and maintenance grows as Factory AI partners with clients to tackle unique challenges