What is a maintenance work order in software?
May 15, 2025
Prevent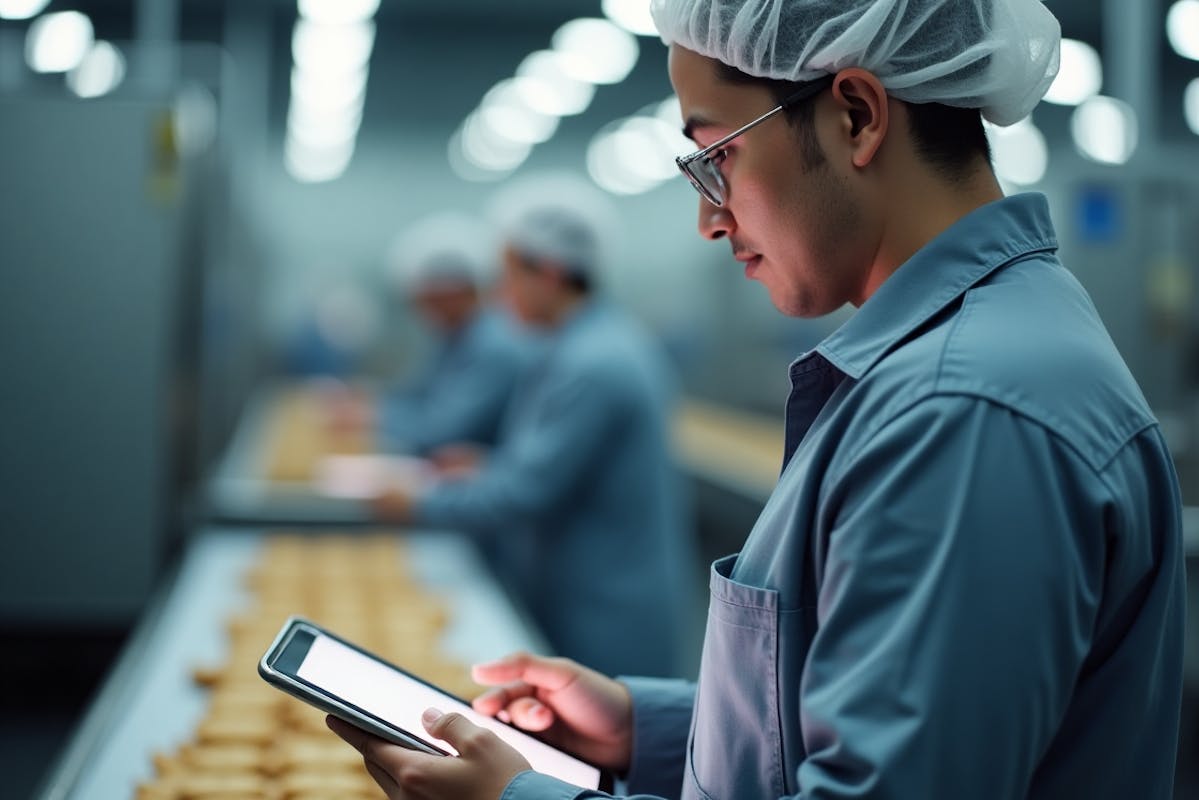
Efficient maintenance is crucial for keeping manufacturing equipment operating at peak performance and avoiding unexpected downtime. A single equipment failure can disrupt production schedules, increase costs, and even compromise workplace safety. To manage maintenance tasks systematically and effectively, organizations rely on maintenance work orders. When these work orders are managed through a Computerized Maintenance Management System (CMMS), they become the backbone of a proactive and organized maintenance strategy. In this article, we’ll explore what a maintenance work order is, its key components, workflow, benefits, best practices for implementation, real-world examples, and common challenges in manufacturing environments.
Definition of a Maintenance Work Order
A maintenance work order is a formal request or instruction to perform maintenance, repair, or inspection tasks on manufacturing equipment or facilities. In a CMMS, work orders are digitally created, tracked, and managed to ensure tasks are completed efficiently and equipment uptime is maximized.
Key Components of a Work Order
A well-structured maintenance work order in a CMMS typically includes:
- Task Description: Detailed explanation of the maintenance activity.
- Asset Information: Equipment or system requiring attention, including location and identification.
- Priority Level: Urgency based on asset criticality and potential impact on production.
- Assigned Personnel: Technicians or teams responsible for execution.
- Required Parts and Materials: List of necessary resources, including inventory status.
- Estimated Labor and Costs: Projected time and expenses.
- Step-by-Step Instructions or Checklists: To ensure consistency and safety.
- Safety and Compliance Notes: Lockout/Tagout (LOTO) procedures, PPE requirements, etc.
- Attachments: Diagrams, manuals, or photos for reference.
- Completion Documentation: Fields for recording actions taken, parts used, and time spent.
Work Order Workflow in a CMMS
The typical workflow for handling maintenance work orders in a manufacturing CMMS includes:
- Task Identification: A maintenance need is detected (e.g., equipment failure, preventive maintenance schedule).
- Request Submission: Maintenance request is submitted via the CMMS.
- Approval: Supervisor reviews and approves the request, converting it into a work order.
- Assignment and Scheduling: Work order is assigned to appropriate personnel and scheduled.
- Execution: Technician performs the task, updating progress in real time (often via mobile devices).
- Documentation: Technician records completed work, parts used, and any observations.
- Closure: Supervisor reviews and closes the work order.
- Analysis: Work order data is analyzed for trends, compliance, and continuous improvement.
Benefits of Work Orders in Manufacturing CMMS
Implementing work order management through a CMMS brings significant advantages:
- Increased Efficiency: Automates and streamlines maintenance processes, reducing paperwork and manual errors.
- Improved Accountability: Tracks who did what, when, and how, ensuring clear responsibility.
- Enhanced Communication: Facilitates collaboration among maintenance, production, and management teams.
- Better Resource Allocation: Optimizes labor, parts, and scheduling.
- Data-Driven Decisions: Provides analytics for identifying recurring issues and optimizing maintenance strategies.
- Regulatory Compliance: Maintains detailed records for audits and safety inspections.
Best Practices for Implementation
To maximize the effectiveness of work order management in manufacturing CMMS, consider these best practices:
- Standardize Work Order Templates: Ensure consistency in information captured for all maintenance types.
- Prioritize Tasks Wisely: Assign priority based on asset criticality, safety, and production impact.
- Attach Checklists and Documentation: Reduce errors and ensure compliance with step-by-step guides.
- Foster Communication: Keep all stakeholders informed of work order status and updates.
- Regular Audits and Reviews: Periodically review work order data for accuracy and process improvement.
- Continuous Training: Equip technicians with up-to-date skills and knowledge of the CMMS.
- Leverage Mobile Access: Enable technicians to update work orders on the go for real-time accuracy.
Real-World Example
A leading automotive manufacturer implemented a CMMS to manage thousands of monthly maintenance work orders. By standardizing work order templates and automating preventive maintenance scheduling, they reduced unplanned downtime by 20%. Technicians used mobile devices to update work orders in real time, ensuring accurate records and faster response times. As a result, compliance with safety inspections improved, and maintenance costs decreased due to better resource planning.
Common Challenges
Despite the benefits, organizations may face challenges such as:
- Incomplete Work Orders: Missing details can lead to delays or improper repairs.
- Resistance to Change: Technicians may be slow to adopt digital systems.
- Data Inconsistency: Lack of standardization can result in poor data quality.
- Overwhelming Backlog: Without prioritization, work orders can pile up, causing critical tasks to be missed.
- Integration Issues: Difficulty connecting CMMS with other enterprise systems (e.g., ERP, inventory).
Conclusion
Maintenance work orders, managed through a CMMS, are essential for efficient, safe, and reliable manufacturing operations. By understanding their structure, workflow, and best practices, and by addressing common challenges, manufacturers can unlock the full potential of their maintenance teams and assets. Effective work order management leads to reduced downtime, improved safety, and optimized maintenance costs-key factors for competitive manufacturing success.
Ready to implement preventive maintenance for your team? Check out Prevent, our newest product here, or if you're looking to implement predictive maintenance, check out Predict here.
